The assignment for this week was to design a 3D mold, machine it, and then use it to cast parts. The most difficult part of this week was thinking about how to design the negative which will be made into the mold that you cast materials into to make the actual object. The object we want to make is limited to the size of the wax block we are given (3.5" x 3" x 1.5"). I originally wanted to make a globe with the continents extruding out. With such a small piece of wax, this may have been to difficult for the shopbot to machine. I settled for a simpler, california outline. First, I imported the vector file into Fusion 360. I was able to use an online JPEG to SVG converter to easily do this. Next, I created a box the size of my piece of wax and another rectangle on top of that to create a "lip" around the area where I will make my mold. Within that rectangle, I placed the outline of California and extruded downwards (to cut into the material).
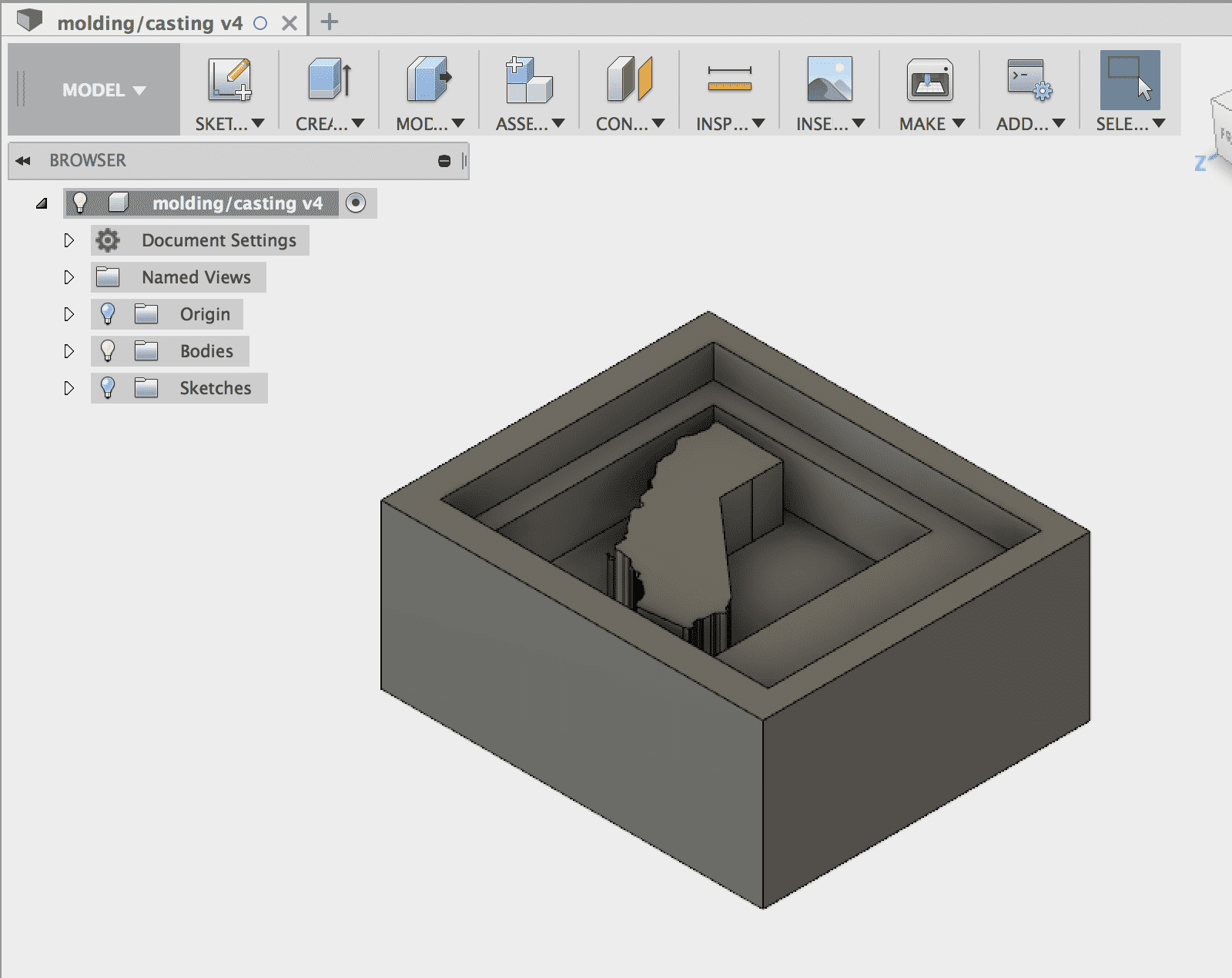
After creating my design in Fusion, I exported the STL into VCarve. After designing the toolpath, rough cut and finish cut, I sent the file to print on the shopbot. First, I needed to hot glue the wax piece onto the wood on the shopbot. Also had to manually zero the shopbot. I had trouble with figuring out which way to orient my wax block. It ended up cutting the long way on my short side but luckily it still fit. However, the first time I tried to cut the negative failed because I loaded both the rough and finish cuts into one tool path. The machine did my finish cut first and then my rough cut, which resulted in a globby mess. I had to redo the piece and also made some edits to my model because there were some regions were the gap was smaller than 1/8", not allowing for the bit to cut through it. My second cut was a success.
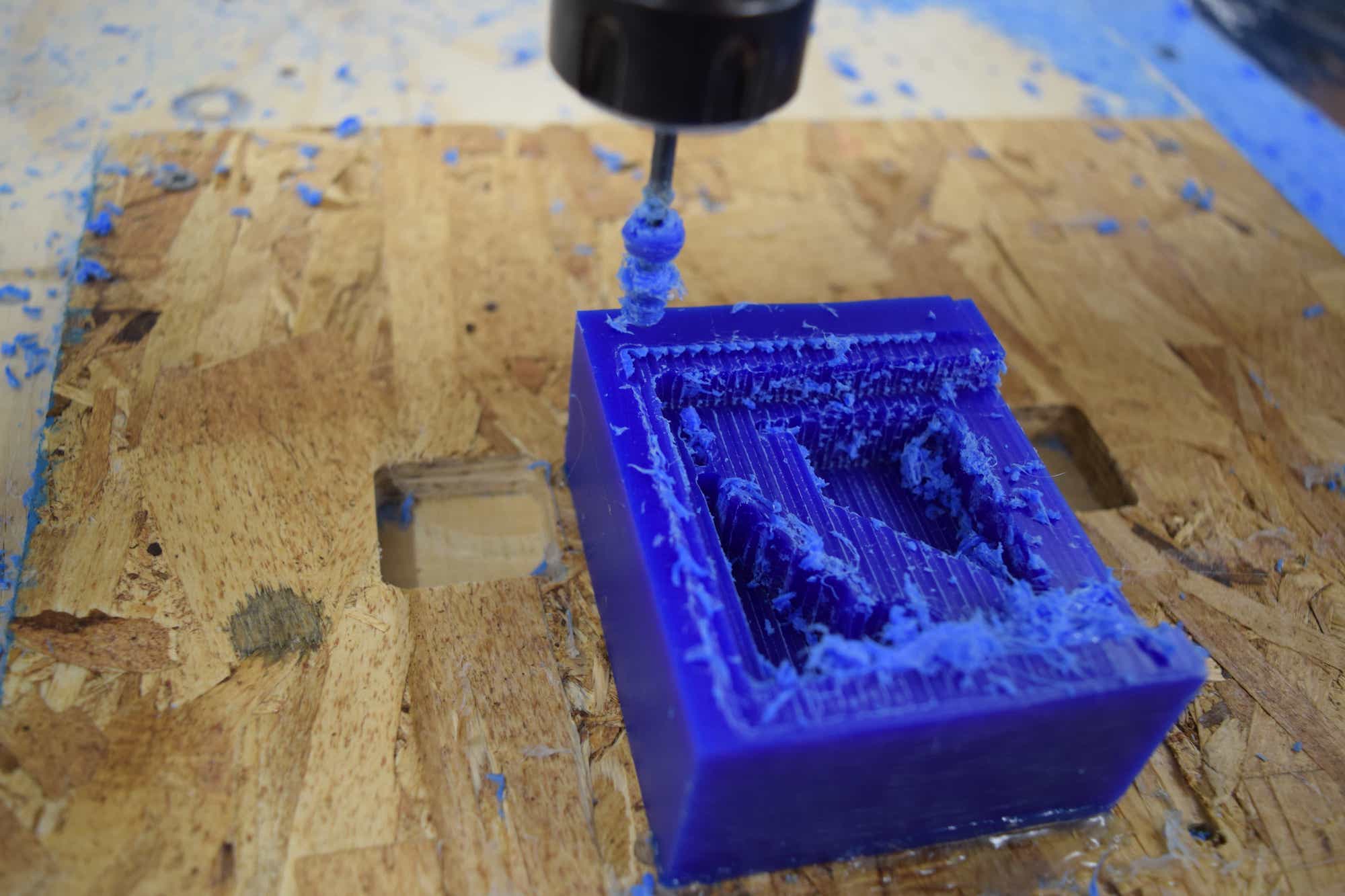
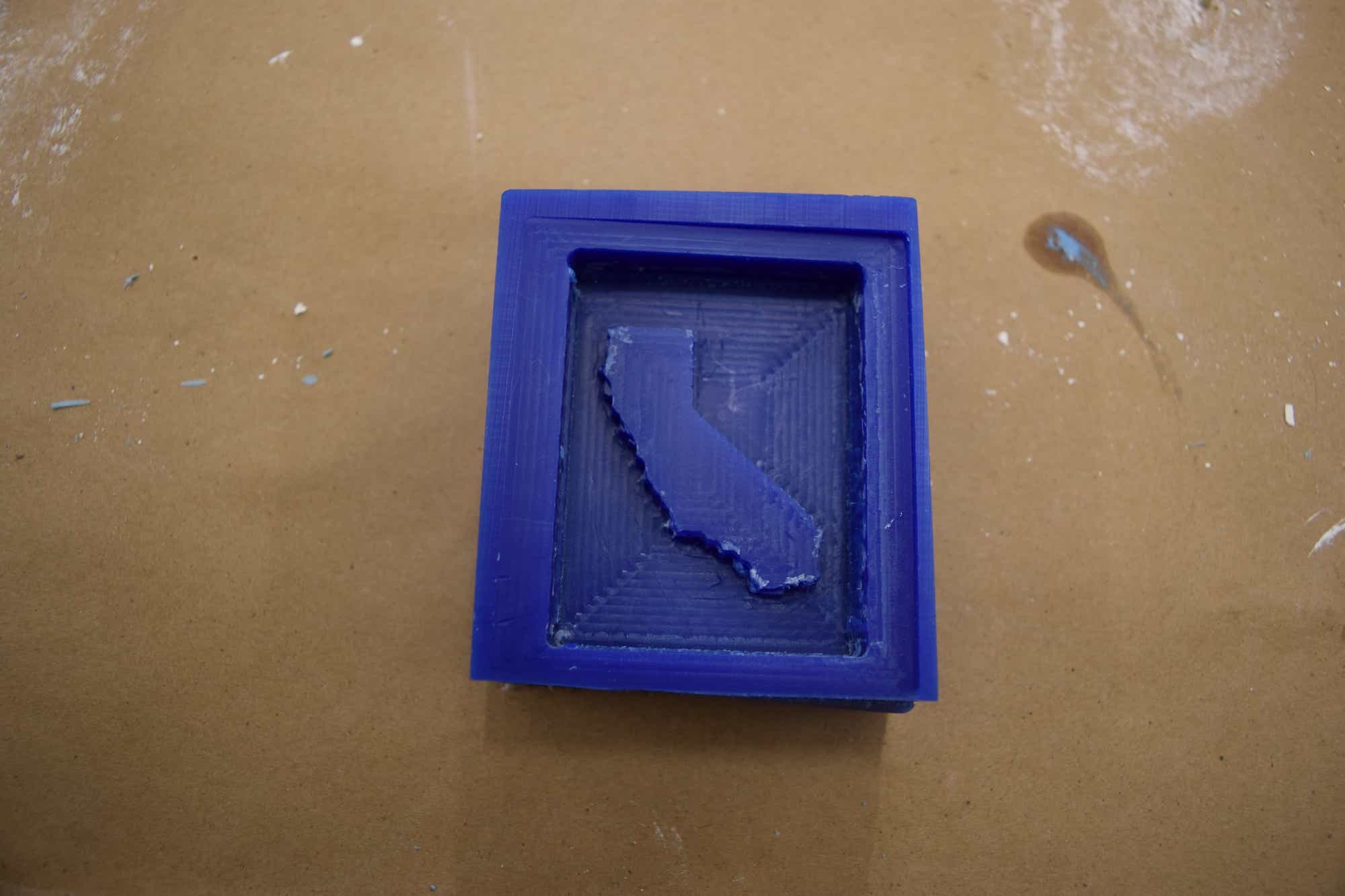
My mold for my mold finished comparitively quickly, I used the 1/8" bit and it completed in about 10 minutes the second time around. I mixed equal parts of the oomoo and poured it into the wax. I let it sit overnight and came back the next day. It was taking more than 90 minutes to dry for most people.
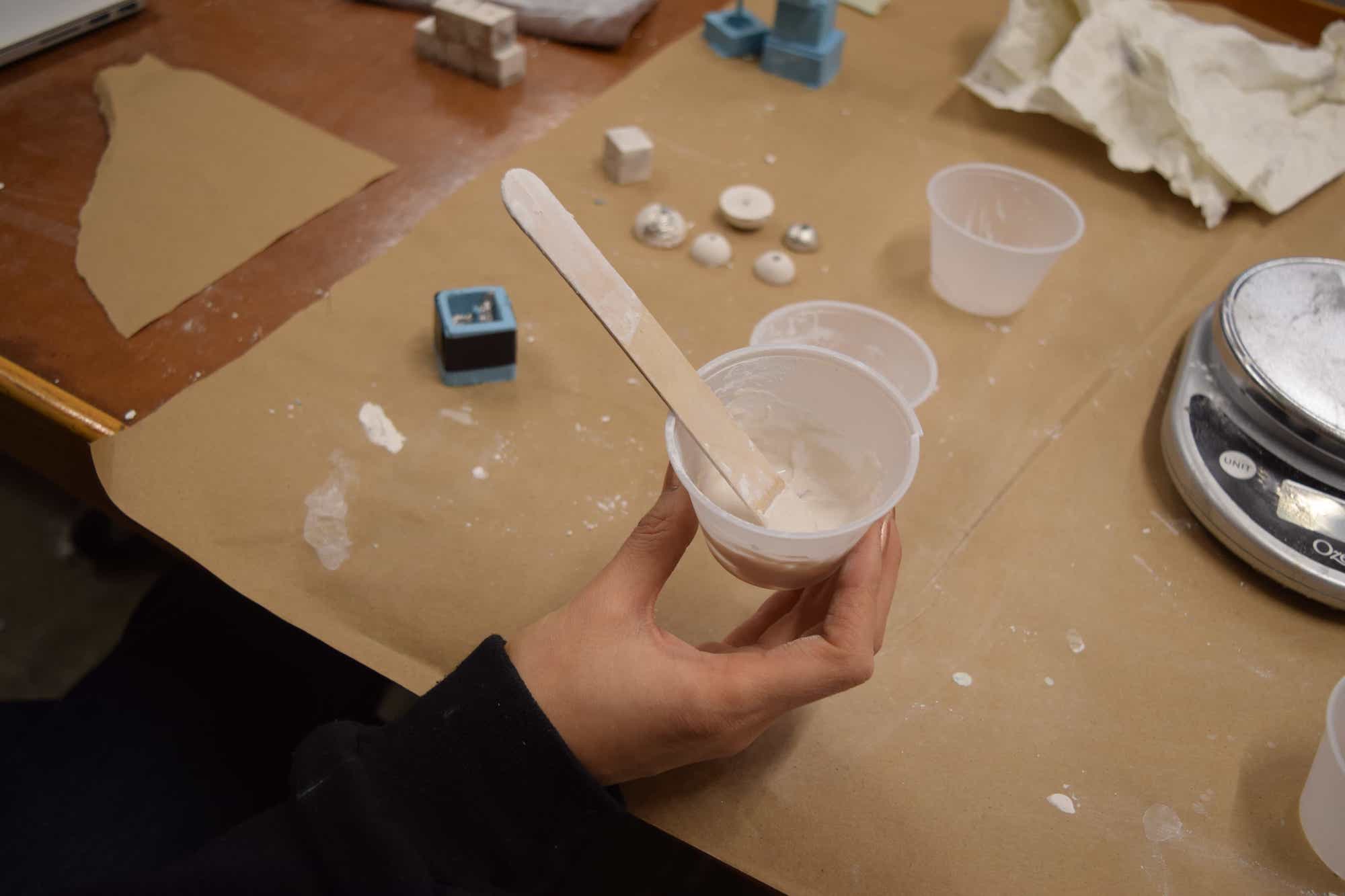
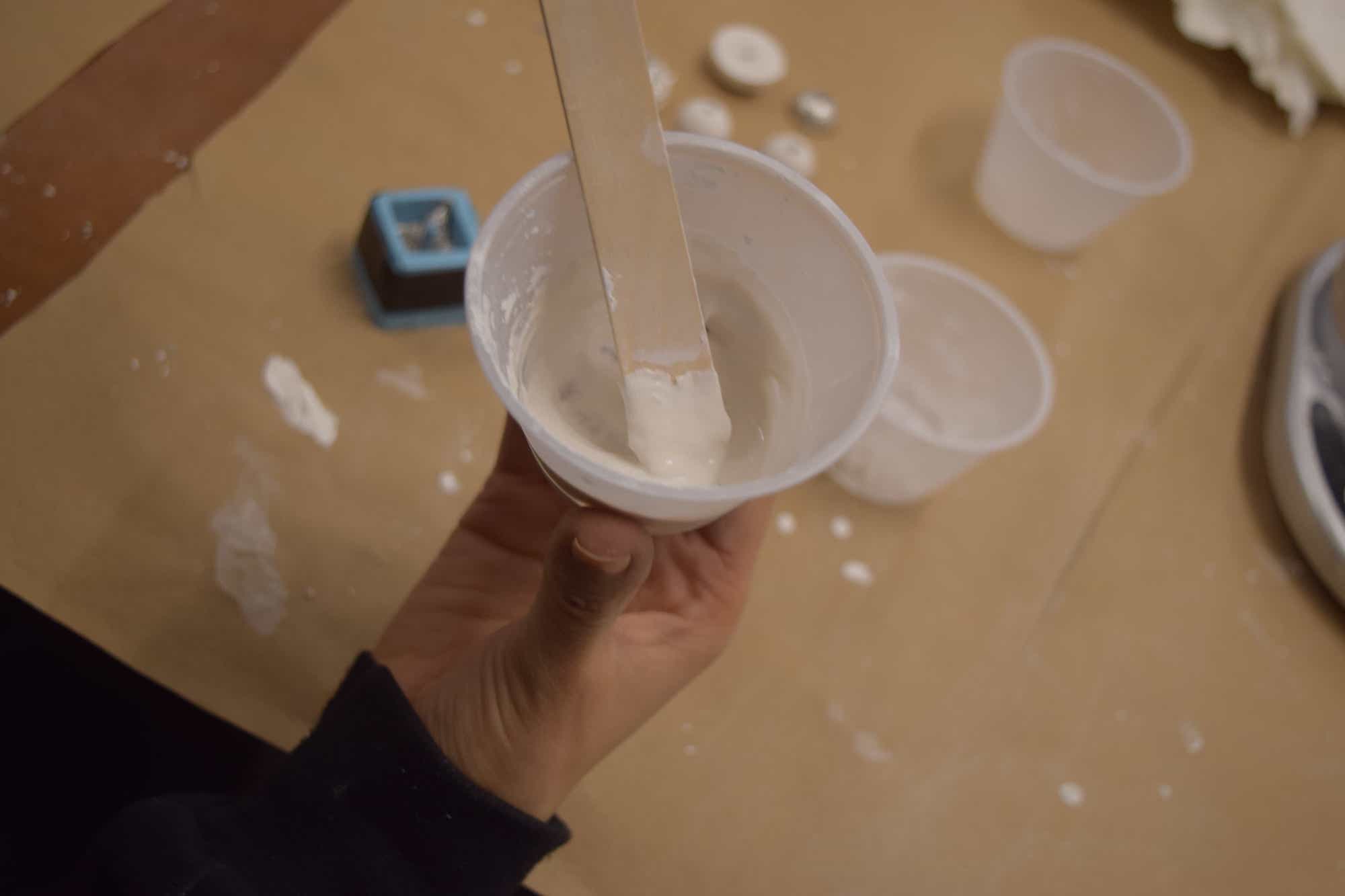
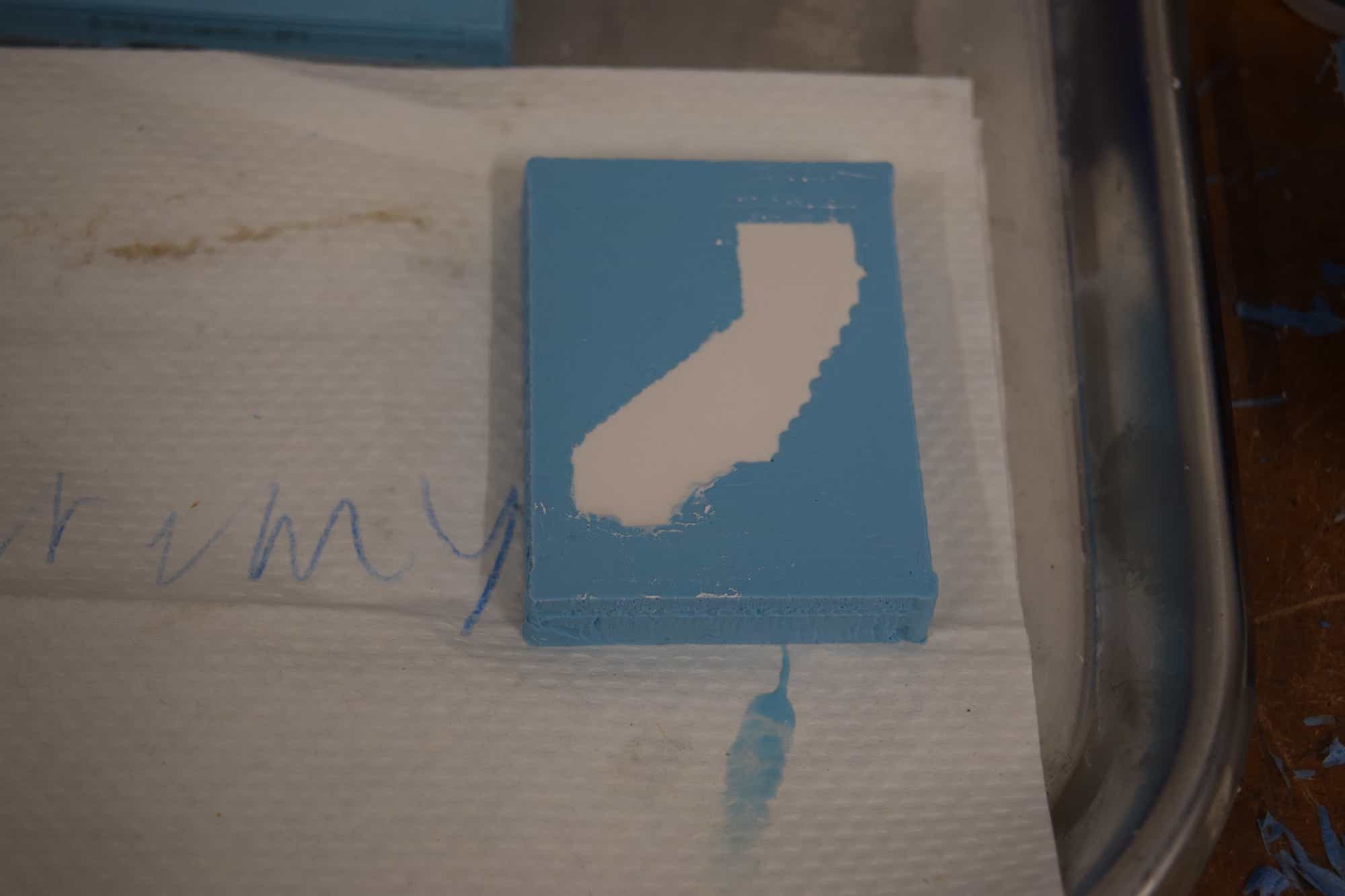
The next day, I mixed .025 lbs of dry stone with .008 lbs of water to make my cast. I poured it in and came back for it in 4 hours. I have a little california paper weight now!