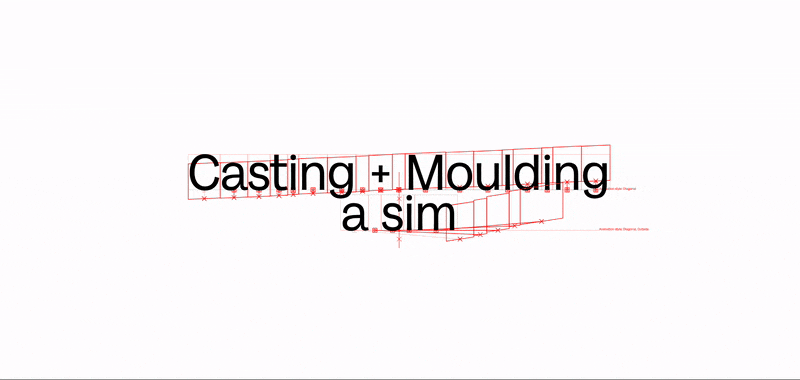
This week we were tasked to cast and mold something...
I wanted my models to be CNC machined out of wax...
I was inspired by several things including film...
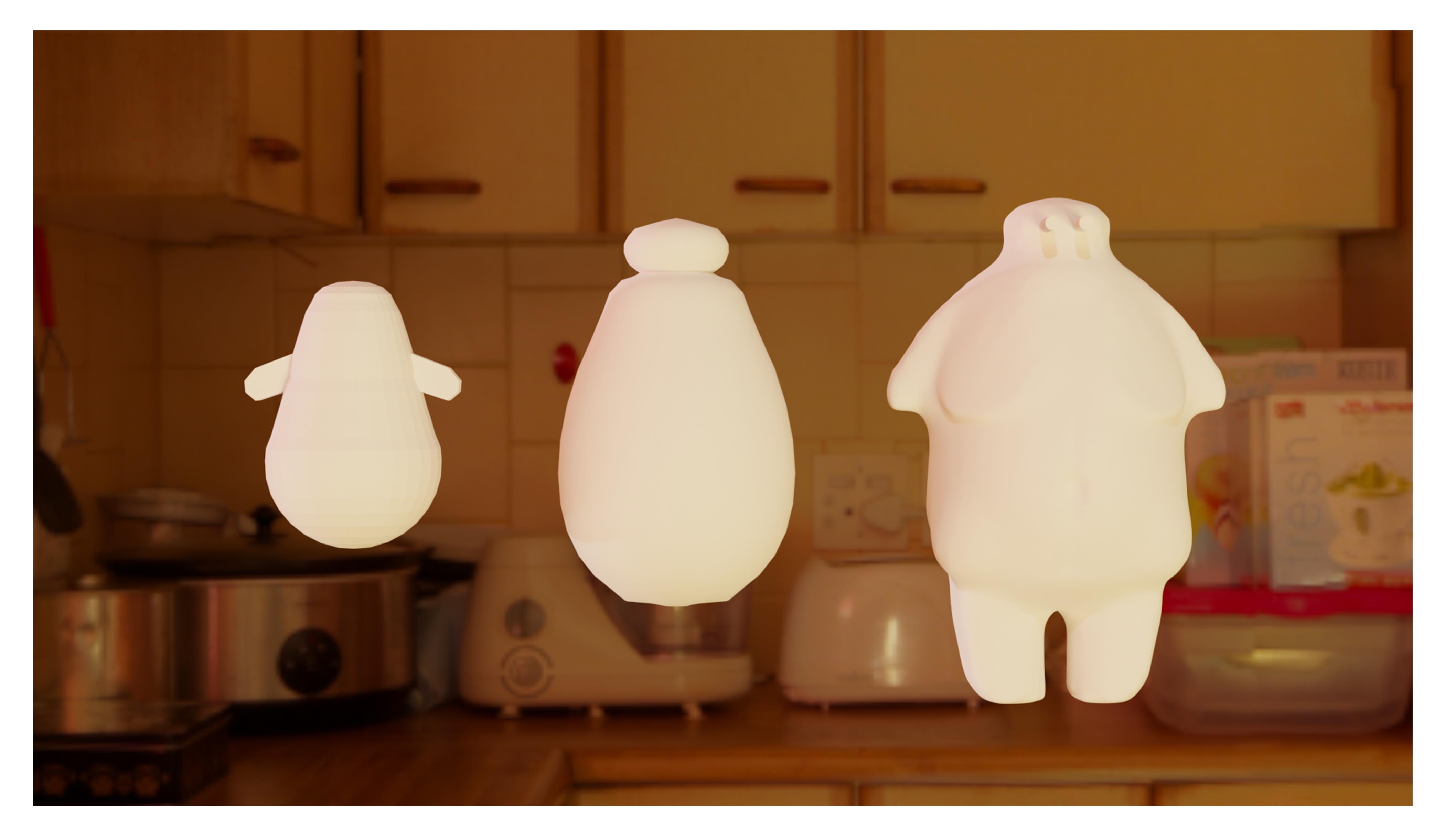
This week we were tasked to cast and mold something...
I wanted my models to be CNC machined out of wax...
I was inspired by several things including film...