Week 10 Composite
This week we need to make something with composite materials. I have never heard of composite before this class. I have been always
thinking of buying a laptop table which I can put on my bed. After the lecture of this week I decided to make one instead of buying one :D
For this session we are using burlap and epoxy. It will create pretty strong materials. The largest problem is, although cured epoxy poses
few health risks, liquid and partially cured epoxies may cause health threats including dermatitis and skin inflammation.
Thus we need to be very careful while working with this chemical. Protection suit, two layers of gloves and even mask will be needed.
During TA session Calvin has showed us steps of mixing the resin and layering up fabric. The ratio of part A and B of epoxy is 100g to 43g,
and the ratio of epoxy to fiber is 3 to 1. Different from what we have done to the oomoo mixing during molding and casting week, this week
we have to be very precise about the quantity since partially cured resin will be dangerous.
Also two spays will be needed: mold releasing and multipurpose adhesive. These two spray cans looks
very similar sometime but they are for totally opposite purpose, so don't mistake these two.
table design
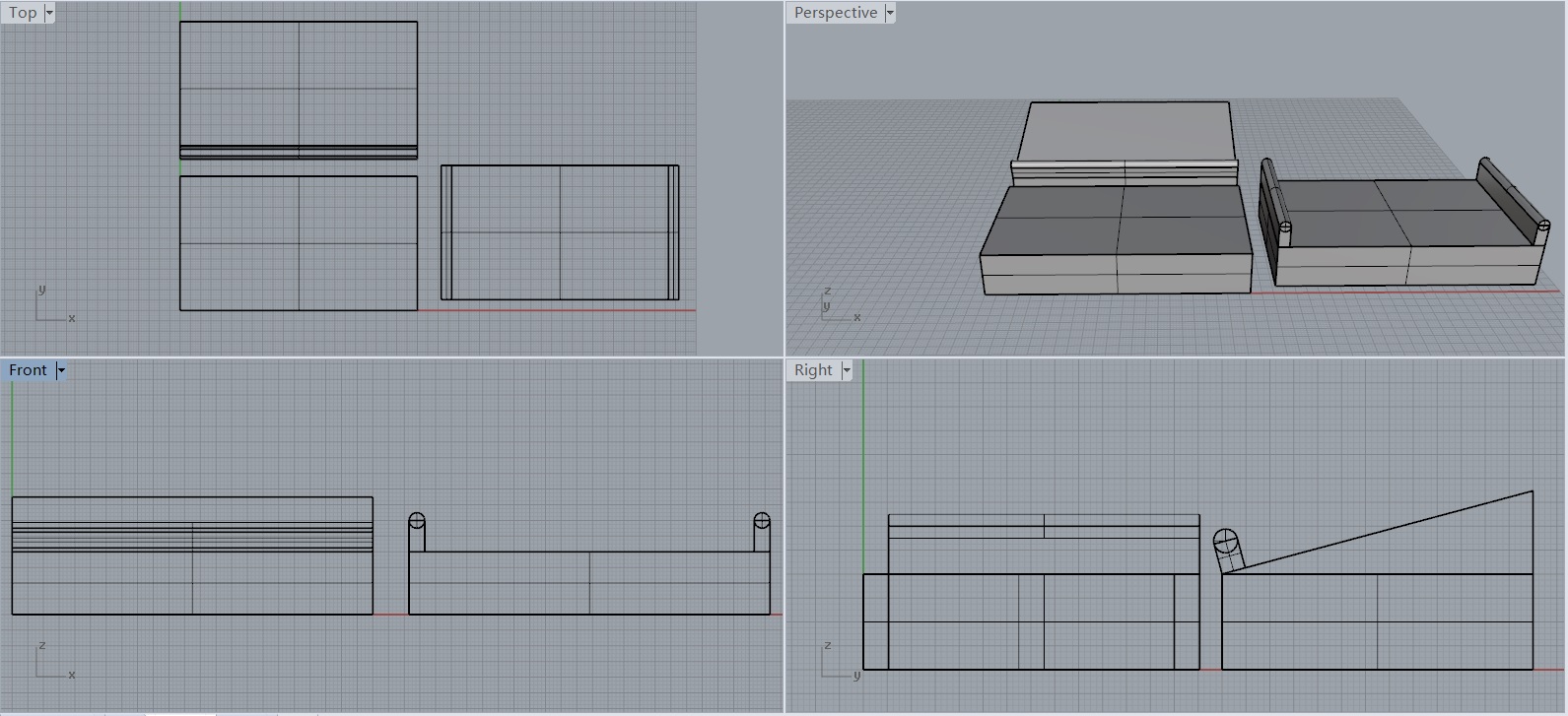

The next day when I woke up I received an email from Christopher cc to all shop users saying that "using yellow wood glue to glue foam will not work. Use the Gorilla glue that looks like dark honey." So I rushed to the shop to check with my foam. Fortunately it seems to work this time in my case so I do not need to re-cut another piece of foam.
Layer up composites
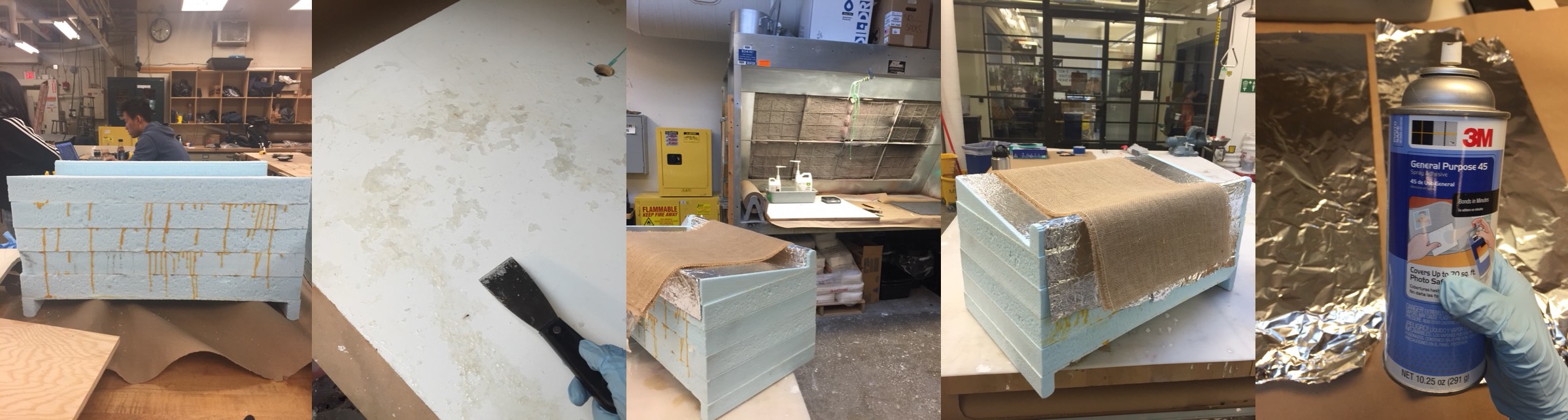
Then Justin came in to supervise me. When he saw my foam piece he said it is too big and we may not have enough epoxy resin left for the whole piece. Maybe we can start from making part of it to get familiar with the process and then I can make the full piece if I still want it later.
So I ended up with just mapping the surface first.
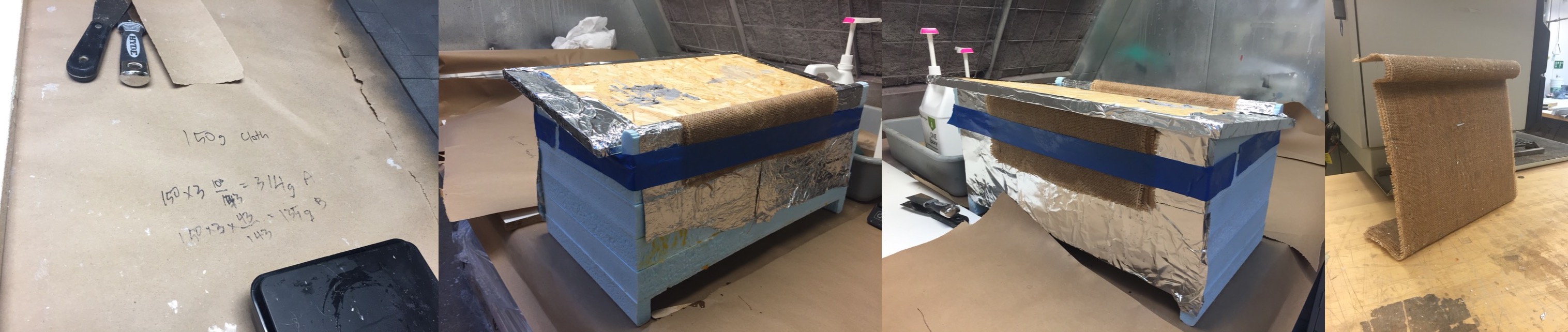
After waiting for a night, I got my "semi" laptop stand!