Project 7: Molding and Casting
This week was all about molding and casting. I was hoping to use an CNC mill to make my molds, but the only mill we had access to was the Roland SRM20 for this week. I despise that thing, and couldnt imagine how long it'd take to machine something with the tiny mills. I relied on old faithful instead: the Prusa Mk4. I decided to see if I could make a solf-plastic fishing lure with a swimming tail.
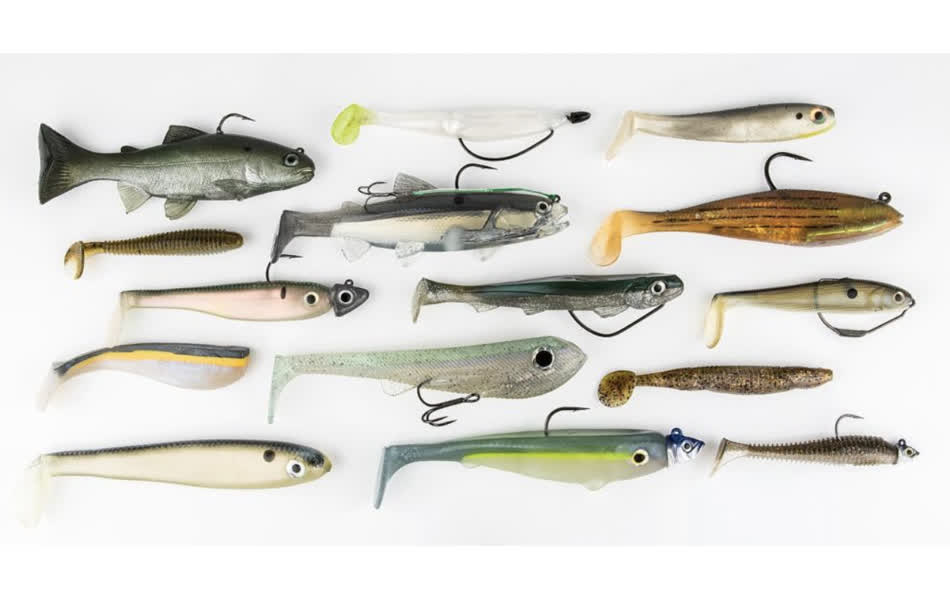
Let's Start with the Group Project
I made little square cups in Solidworks with drafted walls to test the material properties of all the molding and casting materials. The hole in the bottom can be taped over, so that the mold can be pushed out.
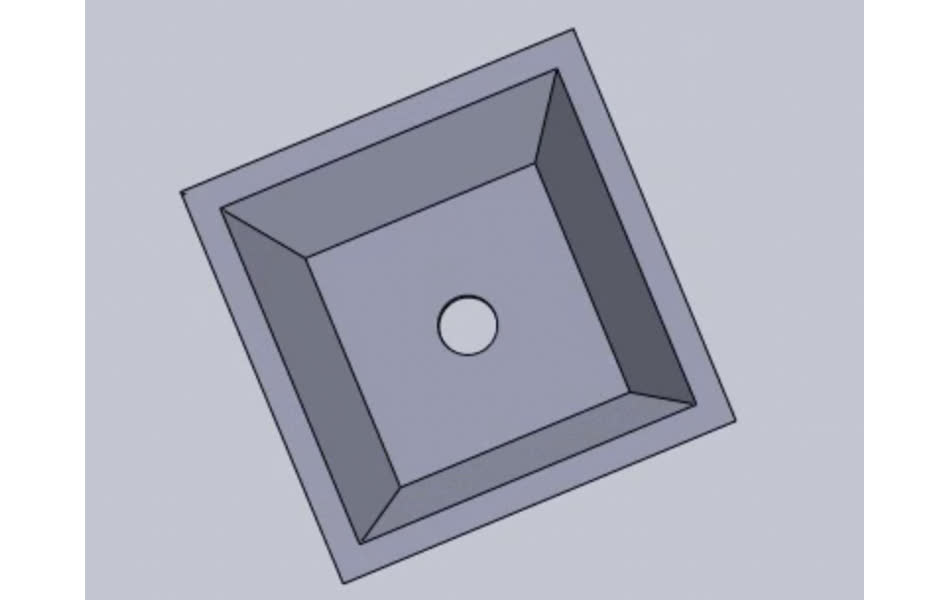
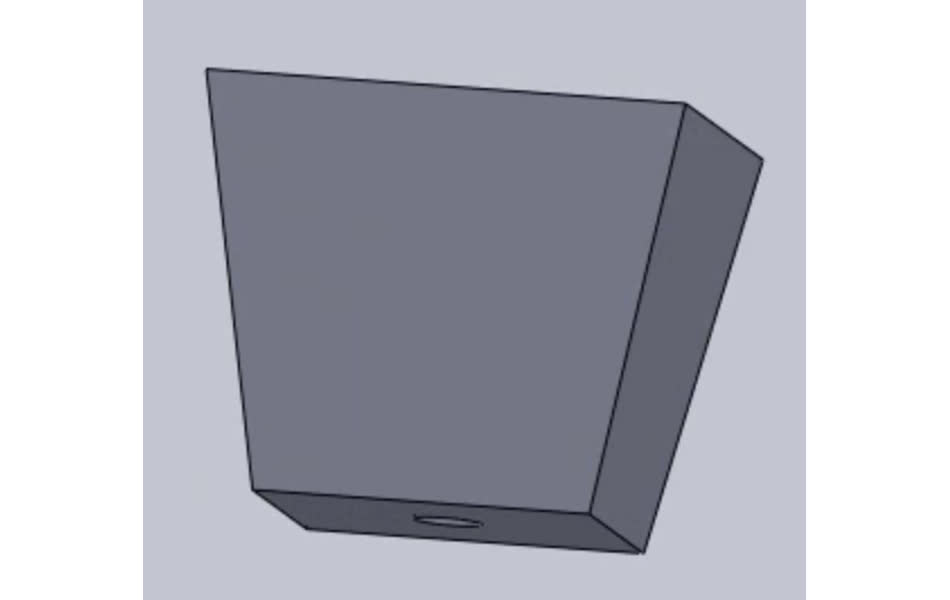
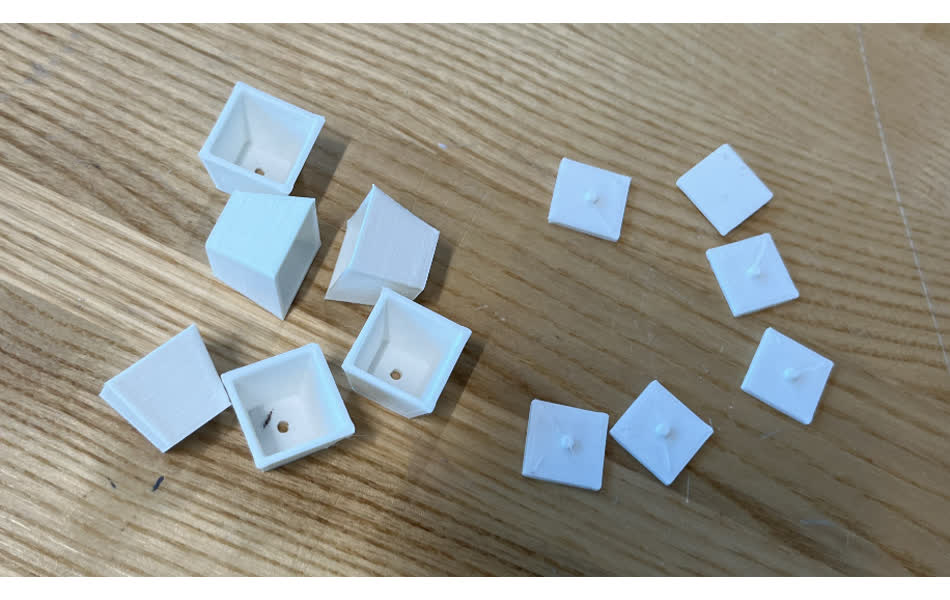
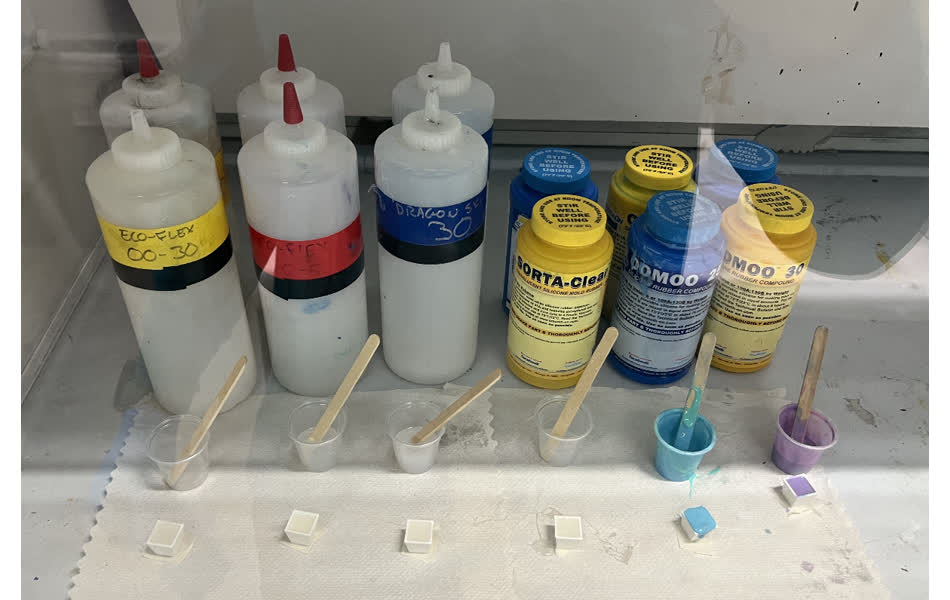
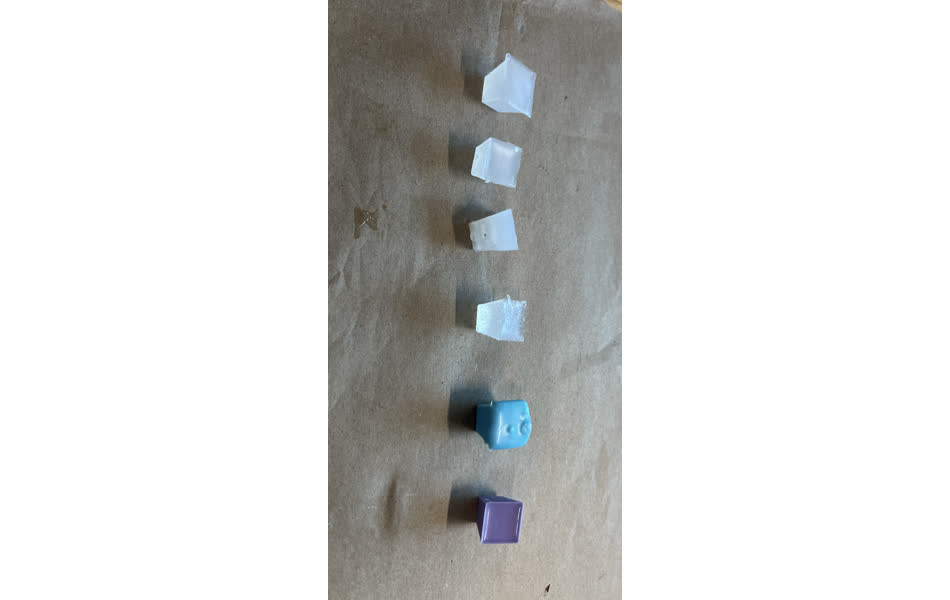
Each material had different stiffnesses. The qualitative ordering was ecoflex 30, ecoflex 50, Dragonskin, Oomoo 25, Oomoo30, softa-clear 37.
Mold-Making Material Comparison
Material | Process | Safety Concerns |
---|---|---|
Ecoflex 30 |
|
|
Ecoflex 50 |
|
|
DragonSkin |
|
|
Oomoo 25 |
|
|
Oomoo 30 |
|
|
Sorta-clear 37 |
|
|
Making the Lure
I started by designing my lure in solidworks by lofting a protrusion between two faces, guided by splines. I kinda just went by what looked right. I also cadded molds, with the hope that I could mill them out.
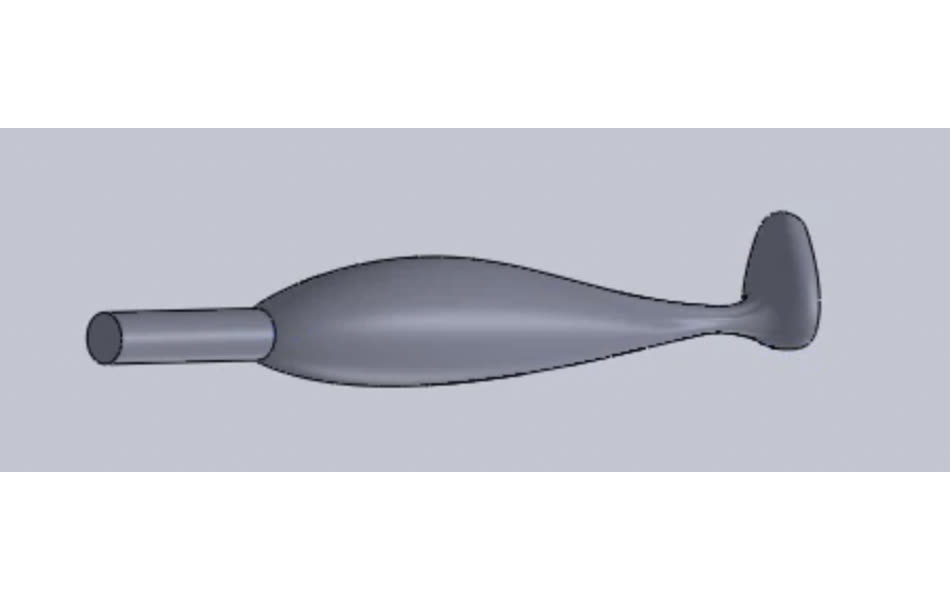
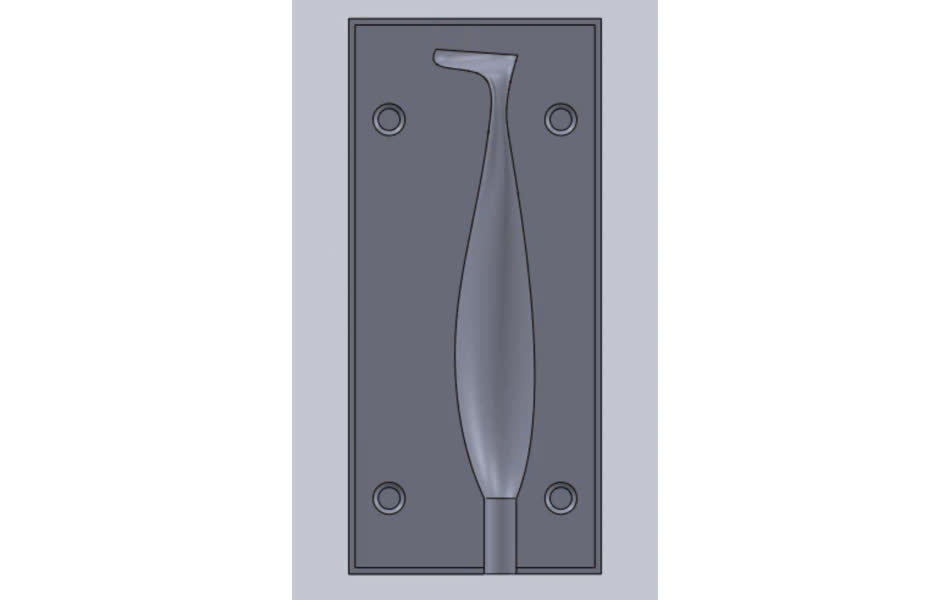
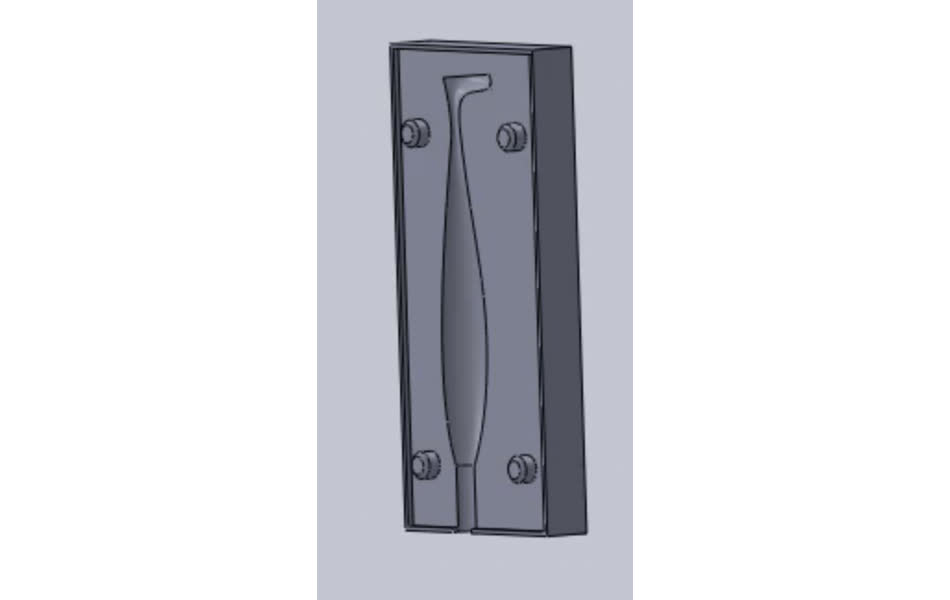
So we didn't have cnc mill capabilities at Harvard. I sold out to the 3D printers.
I thought it would be interesting to print my lure, smooth out print striations, cast around it, then split that cast to make both sides of the mold. Those sides would then be used for making duplicate lures.
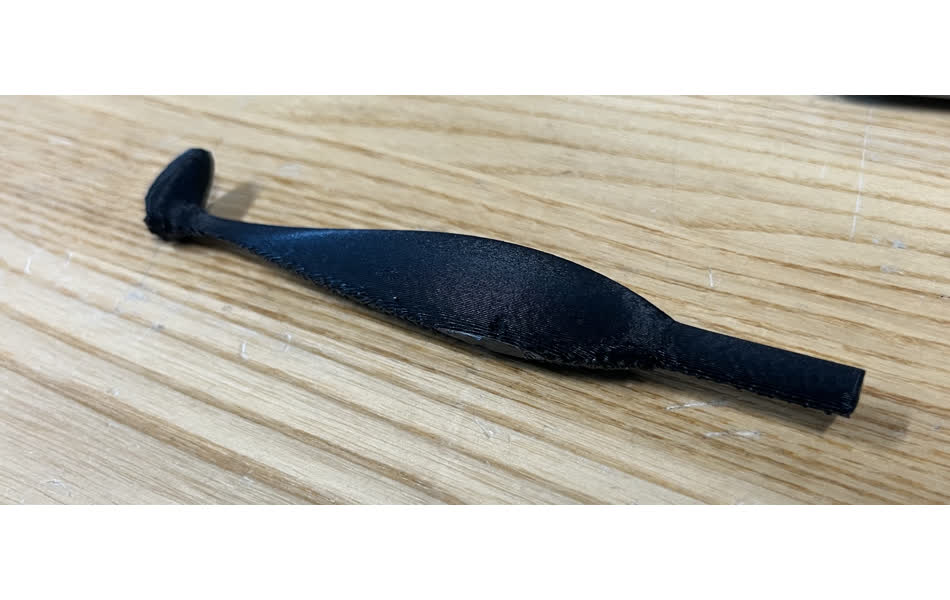
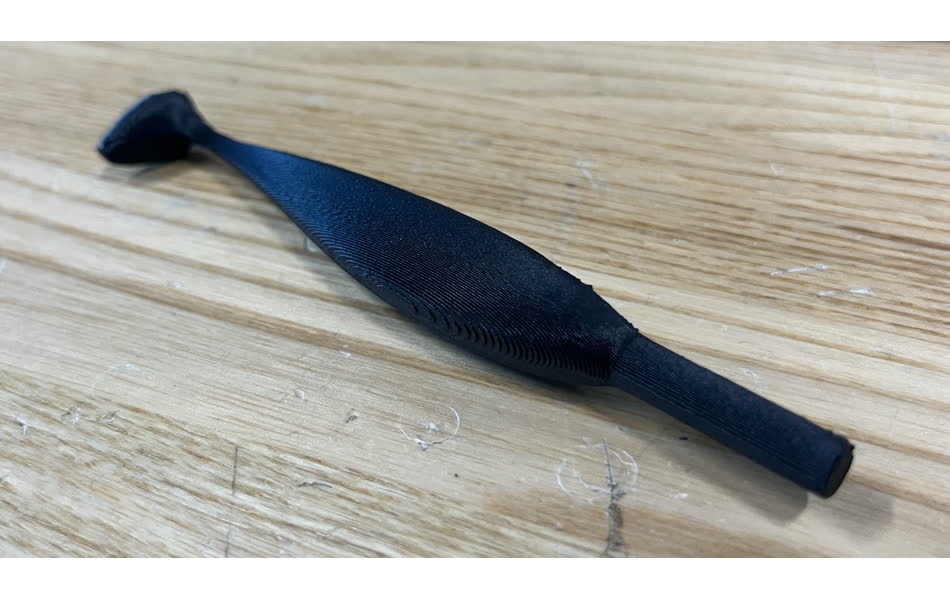
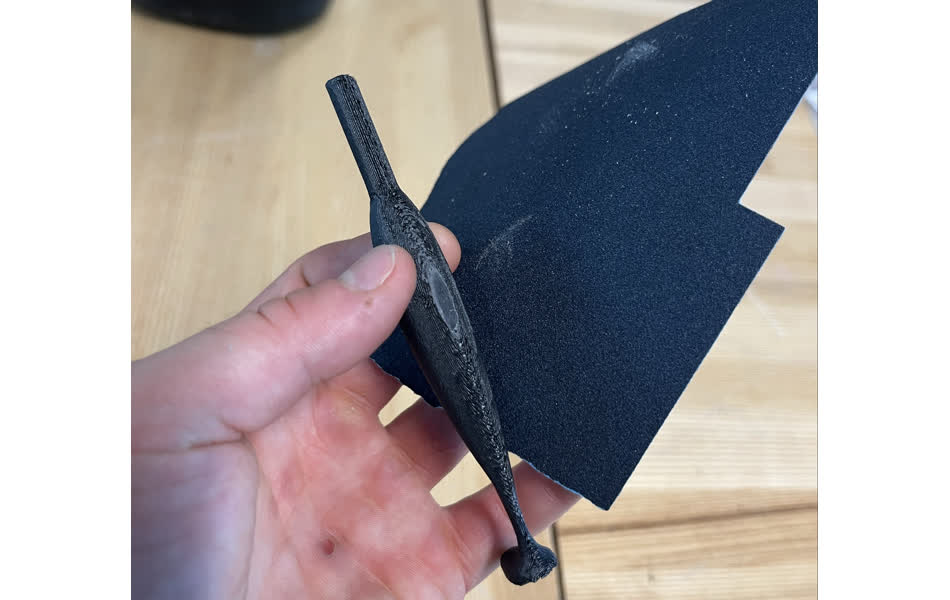
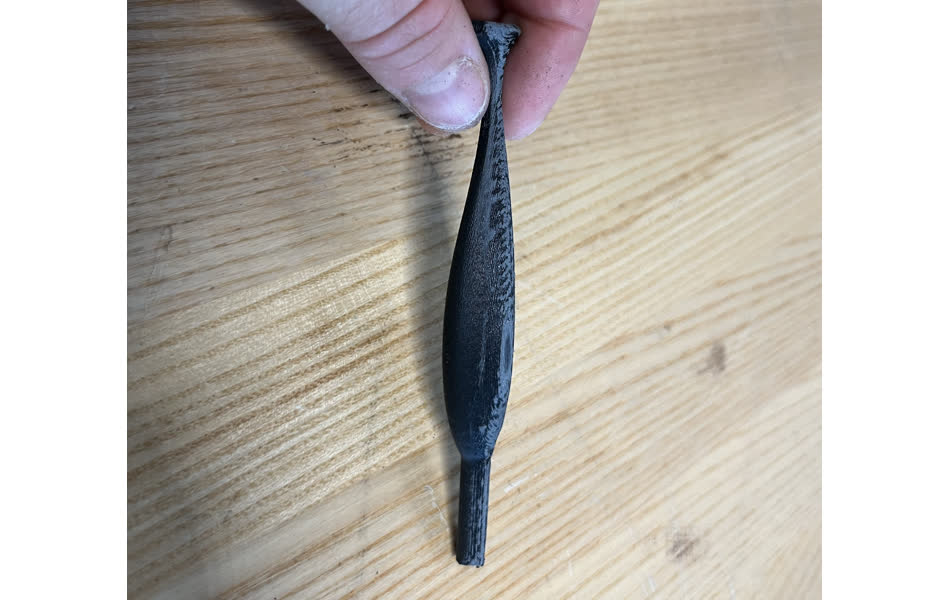
I wanted to try UV epoxy to smooth out the print. The reef had none, and the people in charge suggested superglue. I made a jank cardboard stand (ensuring to use a screwdrive as intended), then proceeded to trash a paintbrush.
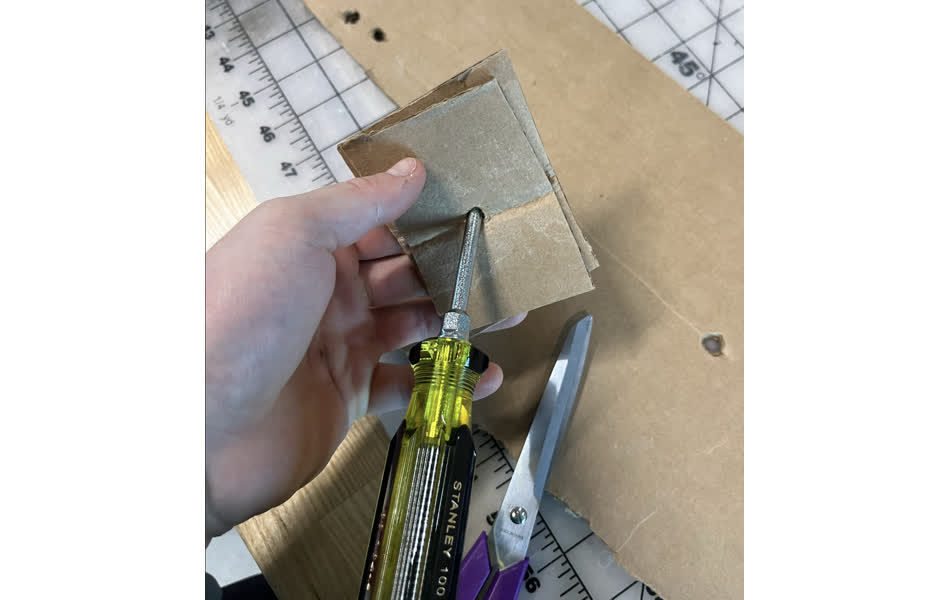
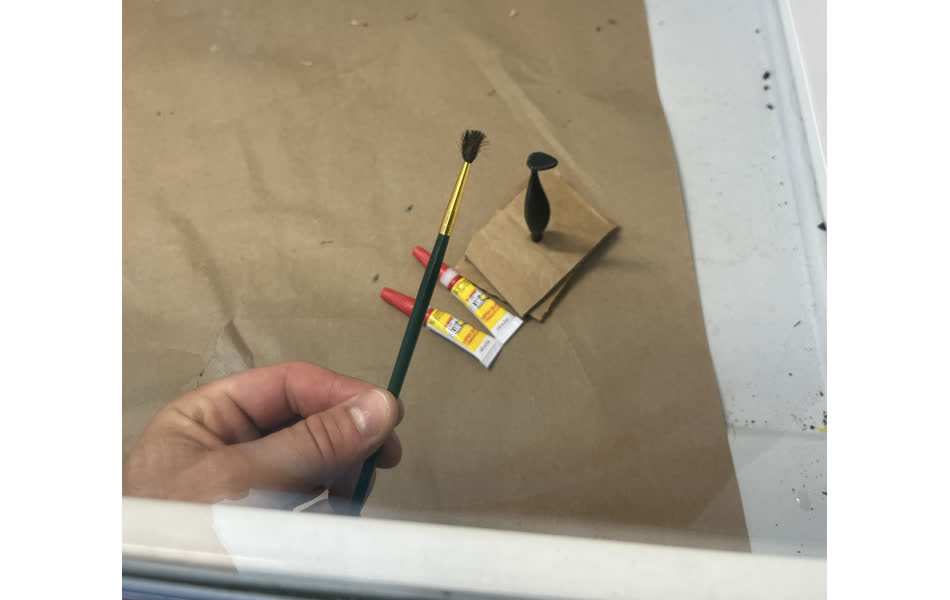
I used my sacrificial paintbrush for two layers, but it still didn't look great.
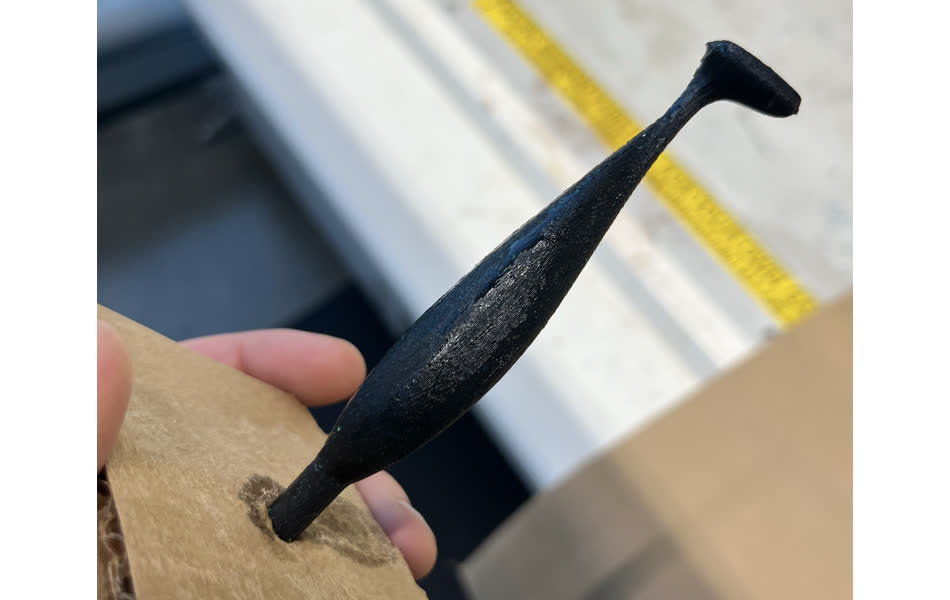
I then rummaged through materials in the casting room, and found the perfect resin: XTC-3D, which is literally used for filling 3D print striations. It worked pretty well.
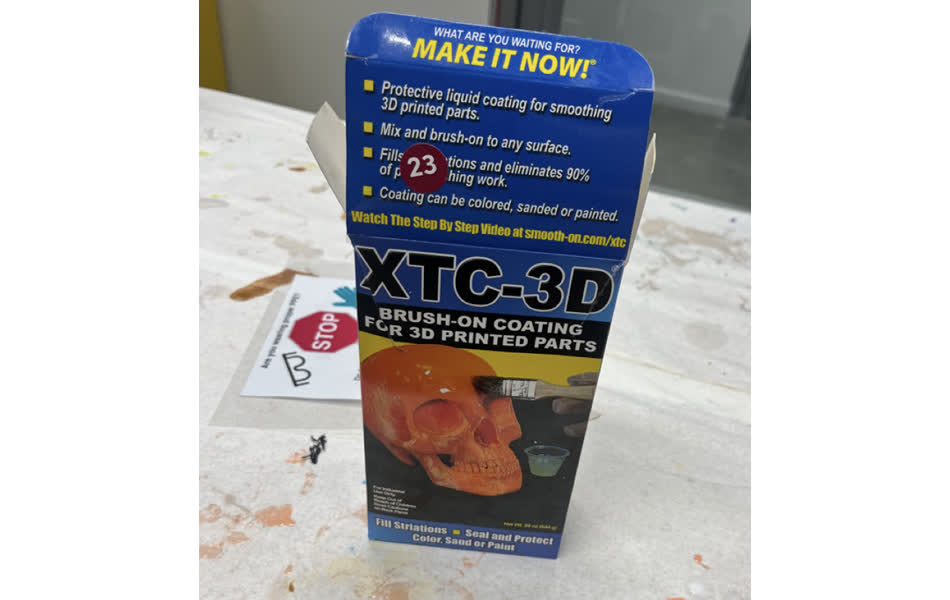
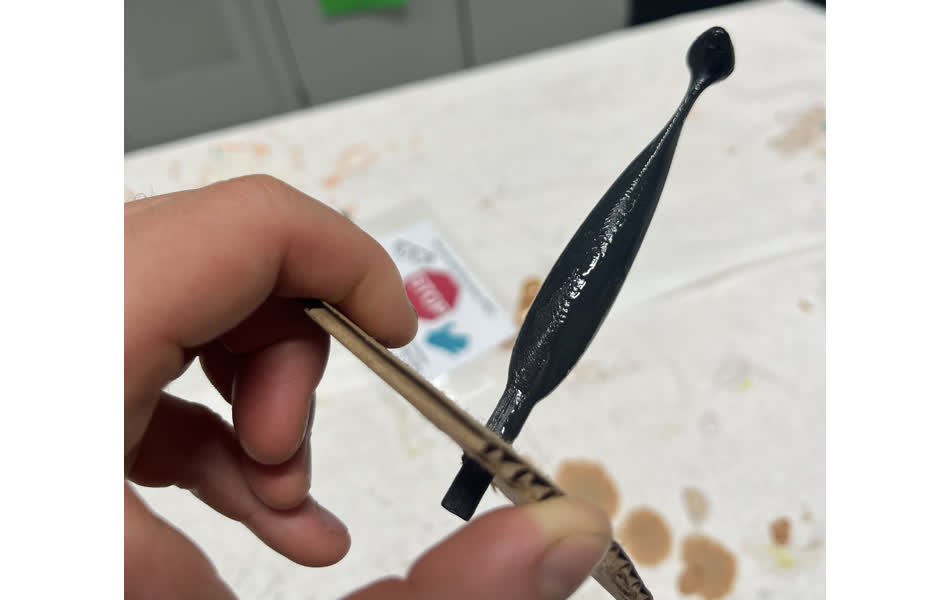
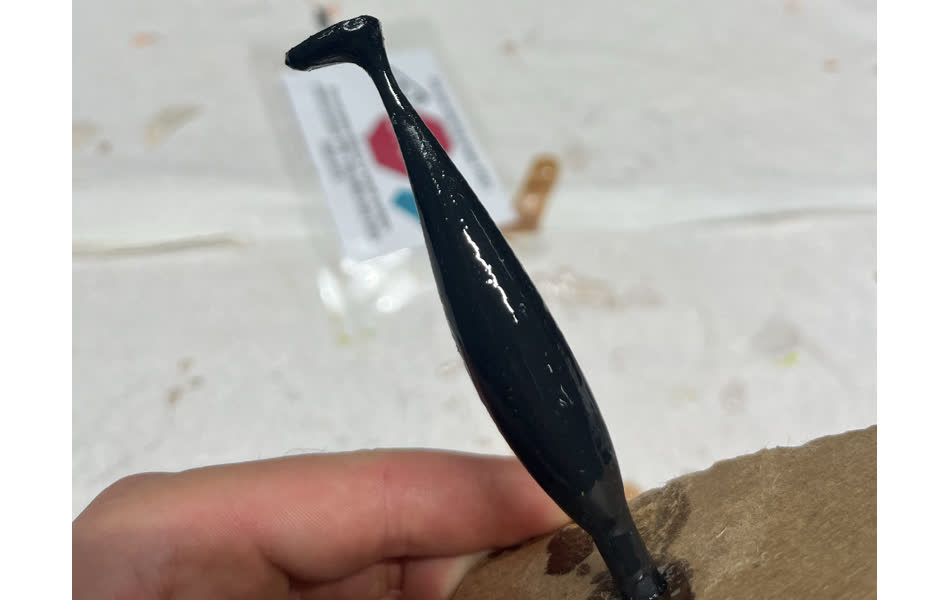
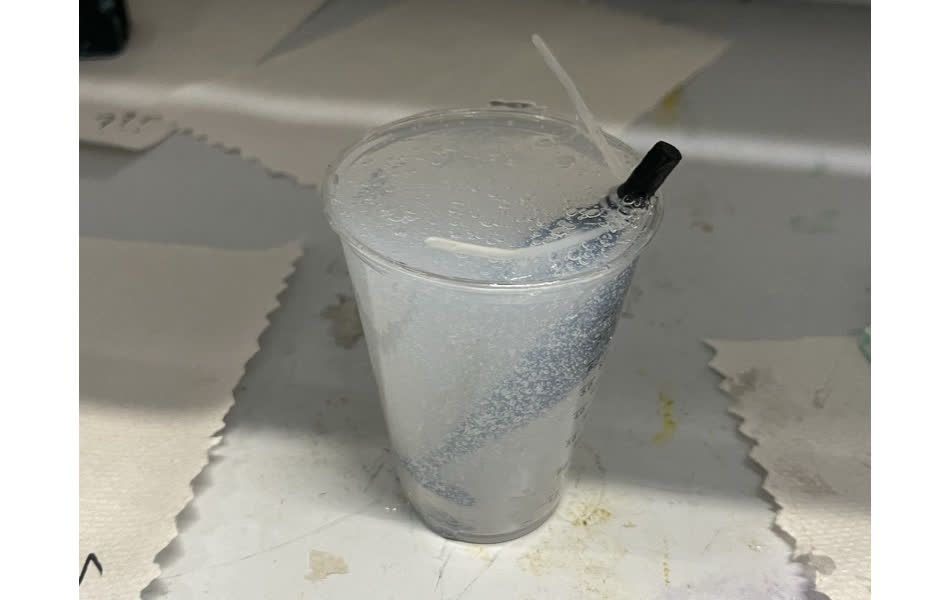
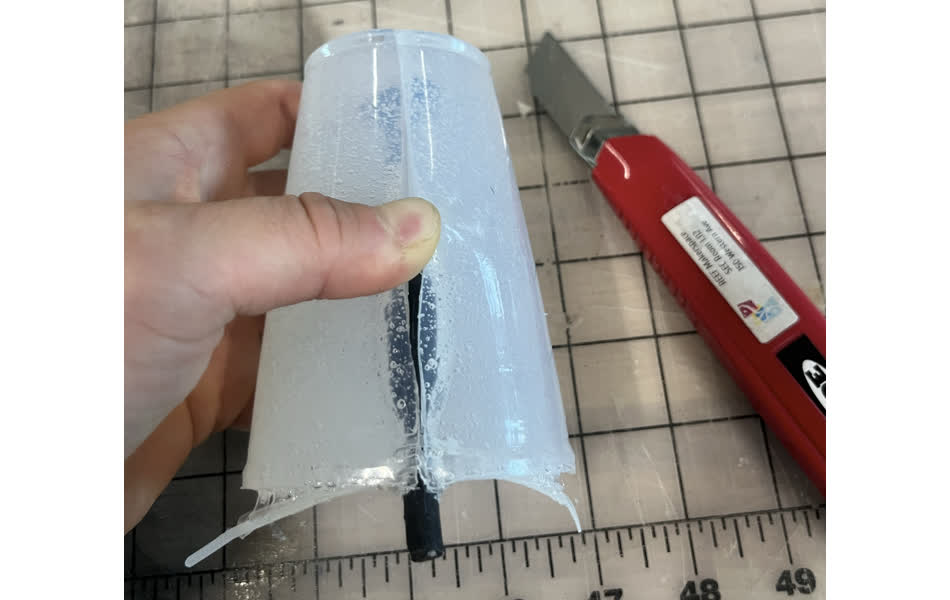
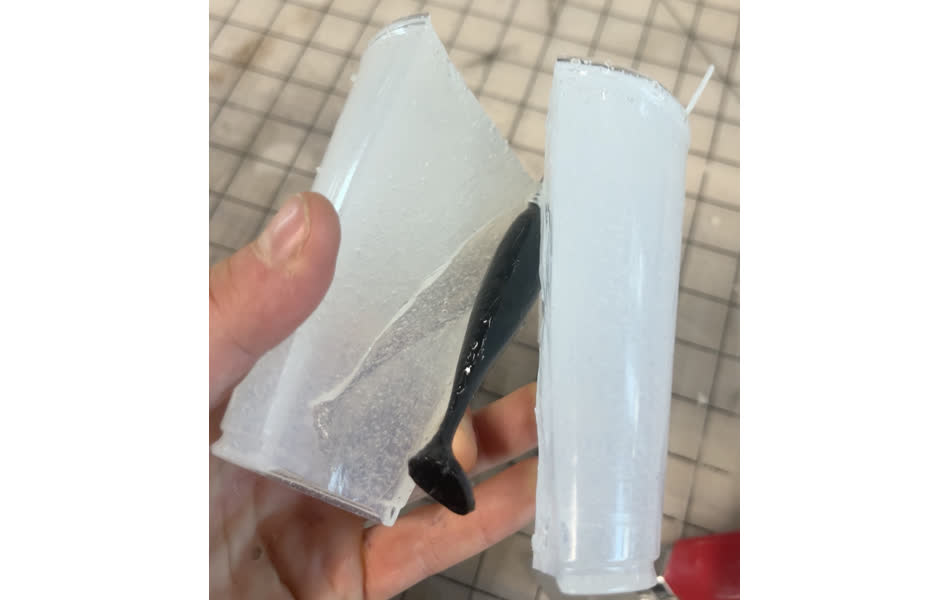
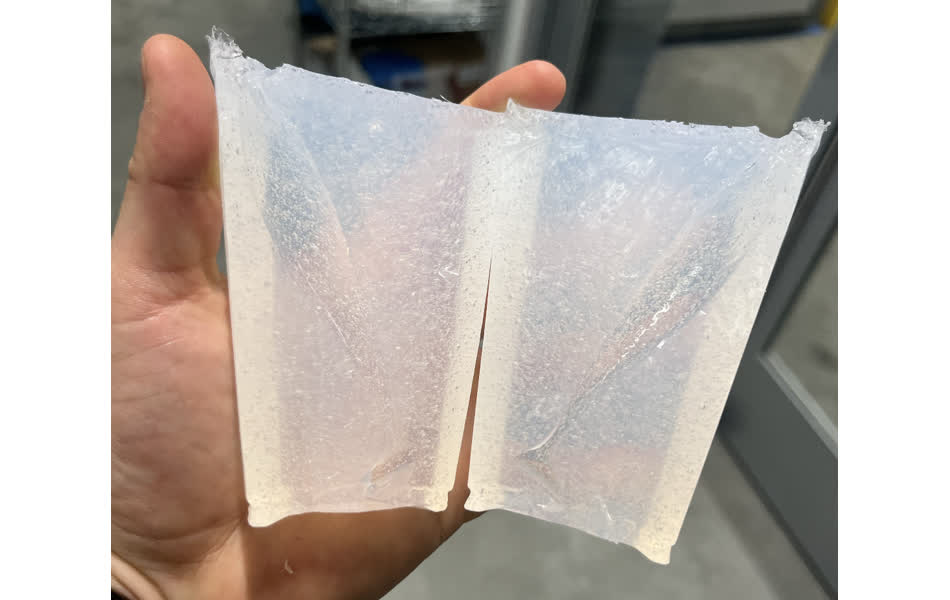
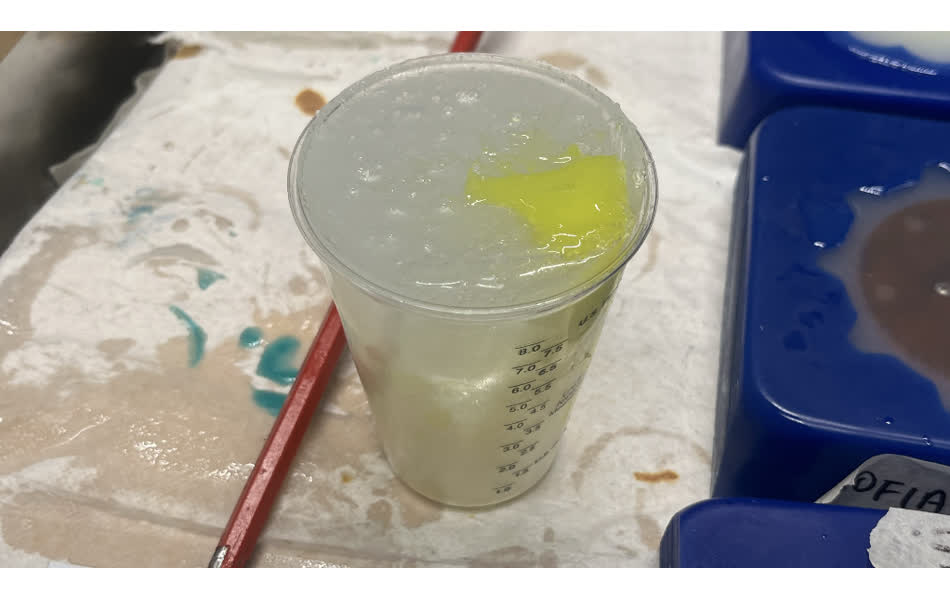
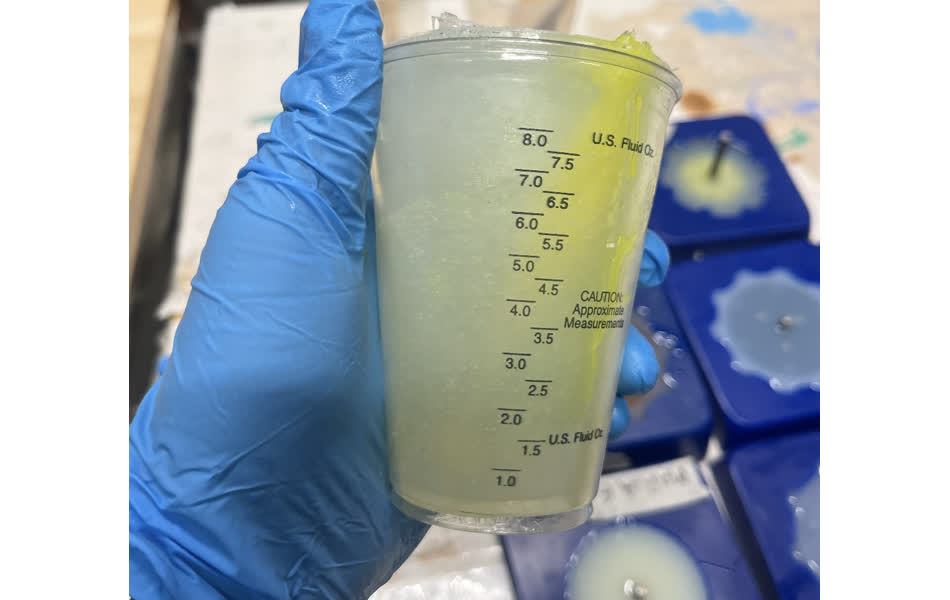
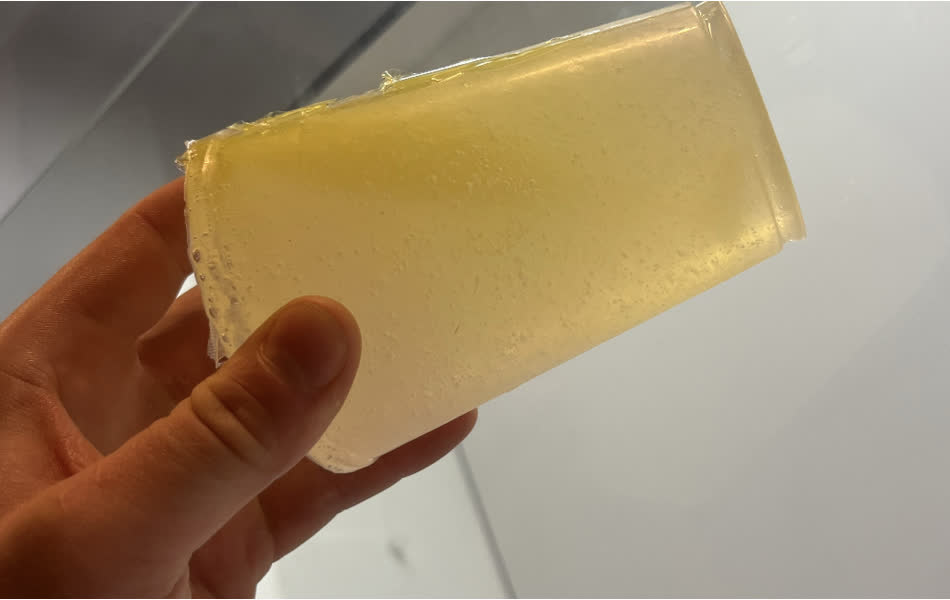
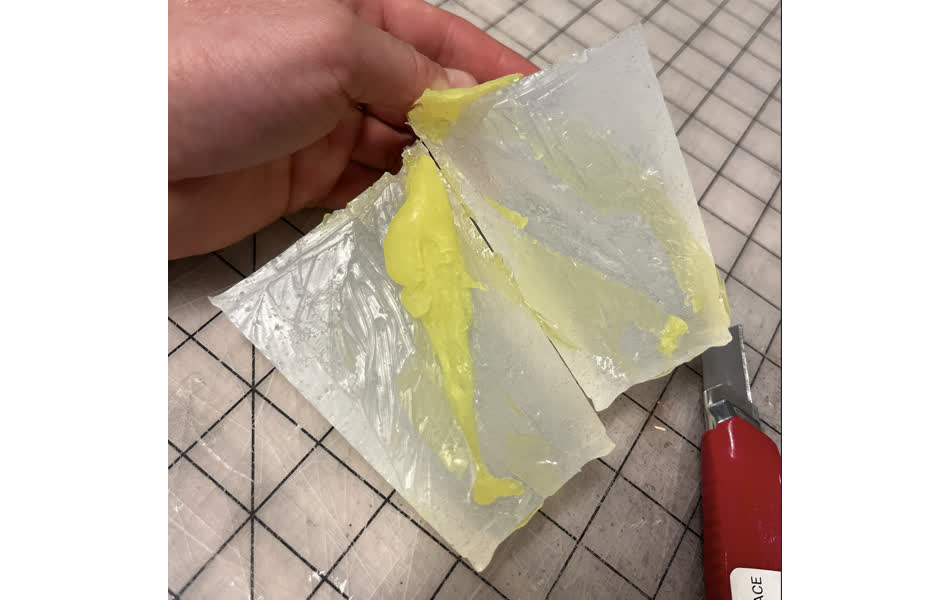
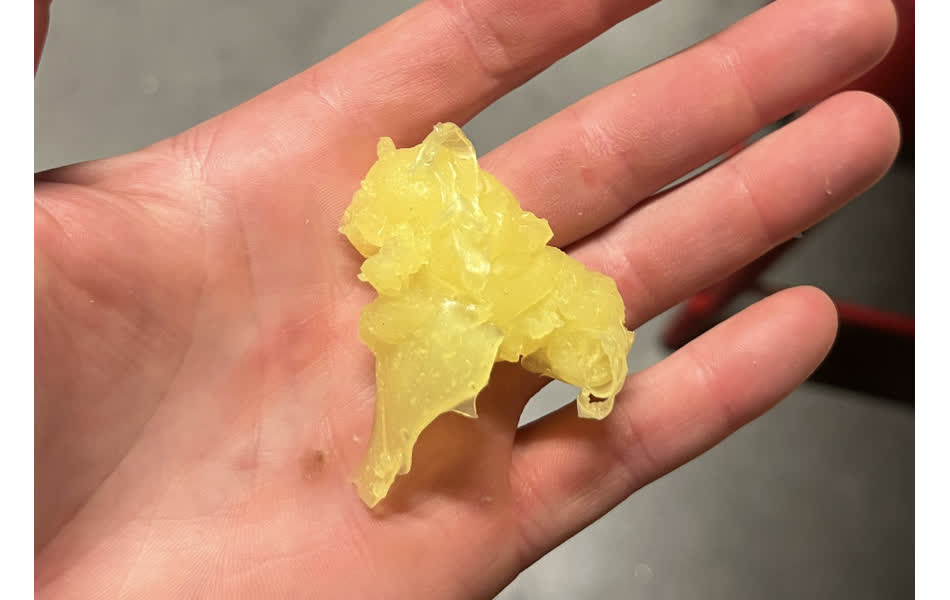
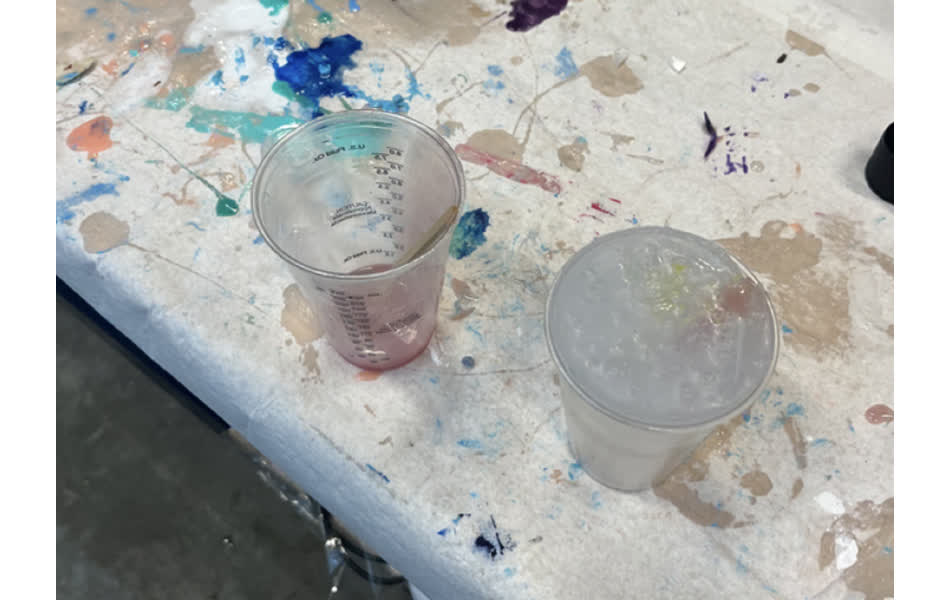
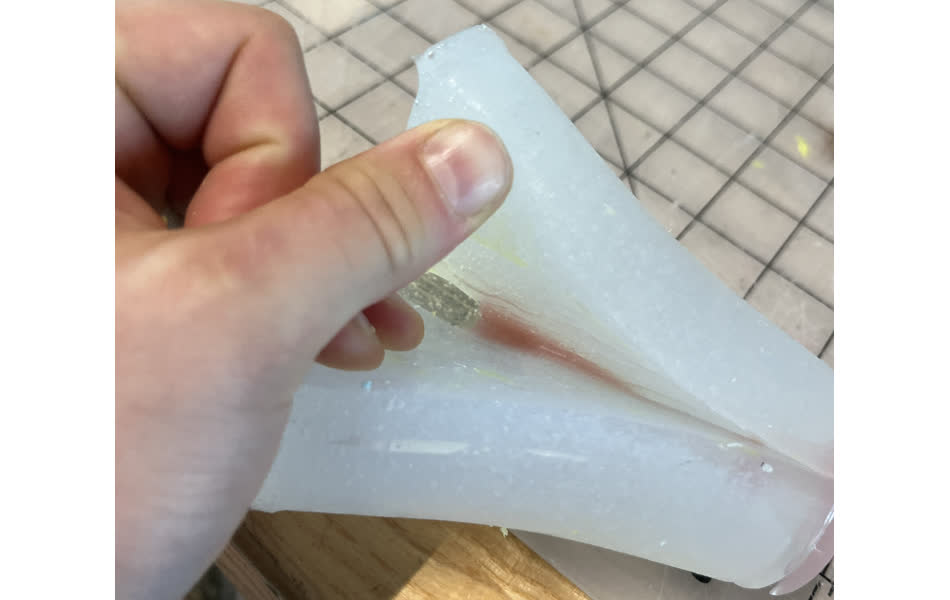
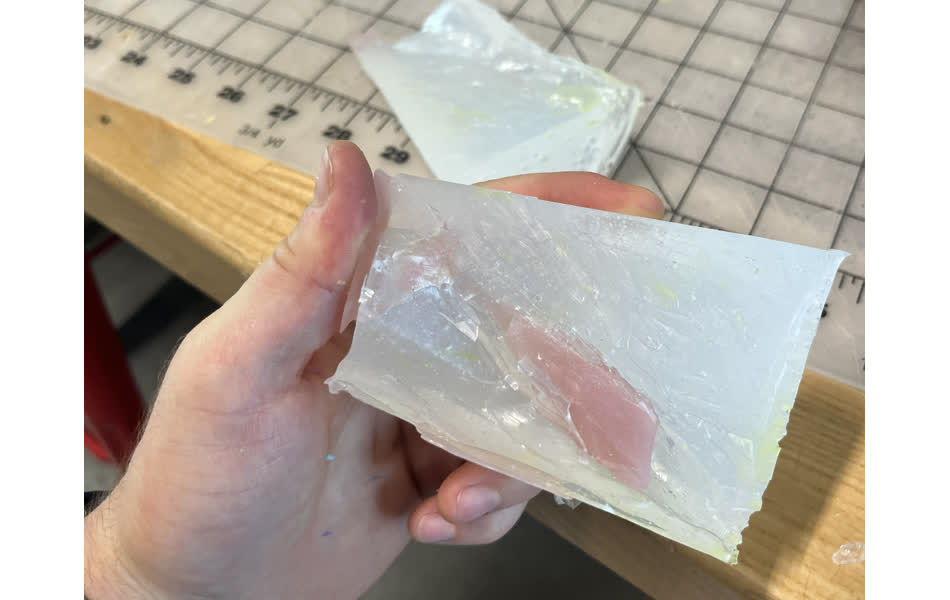
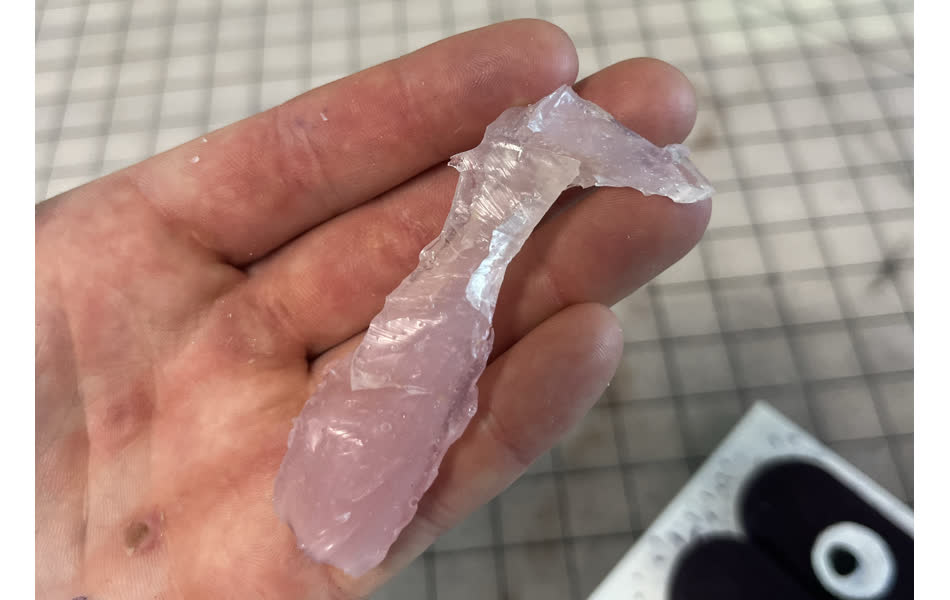
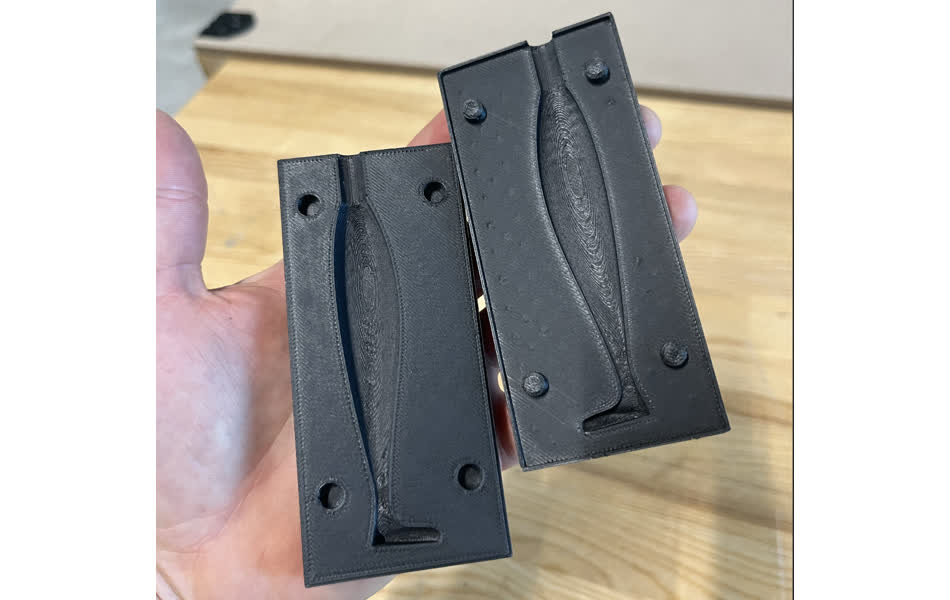
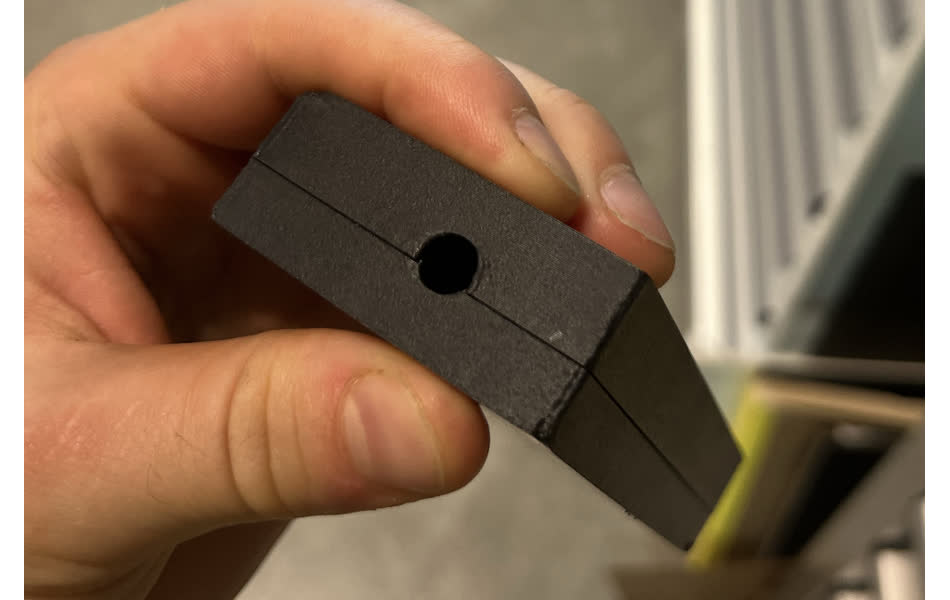
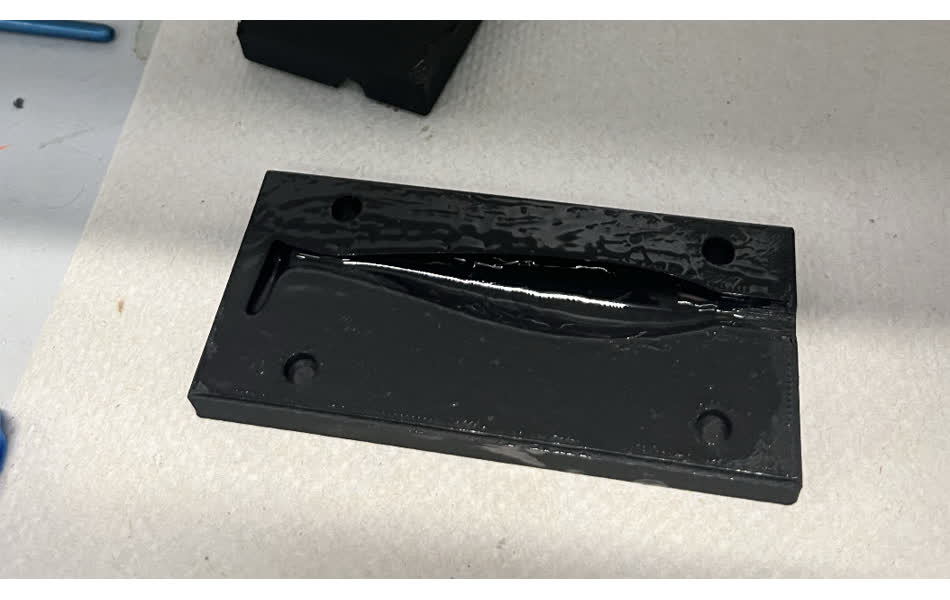
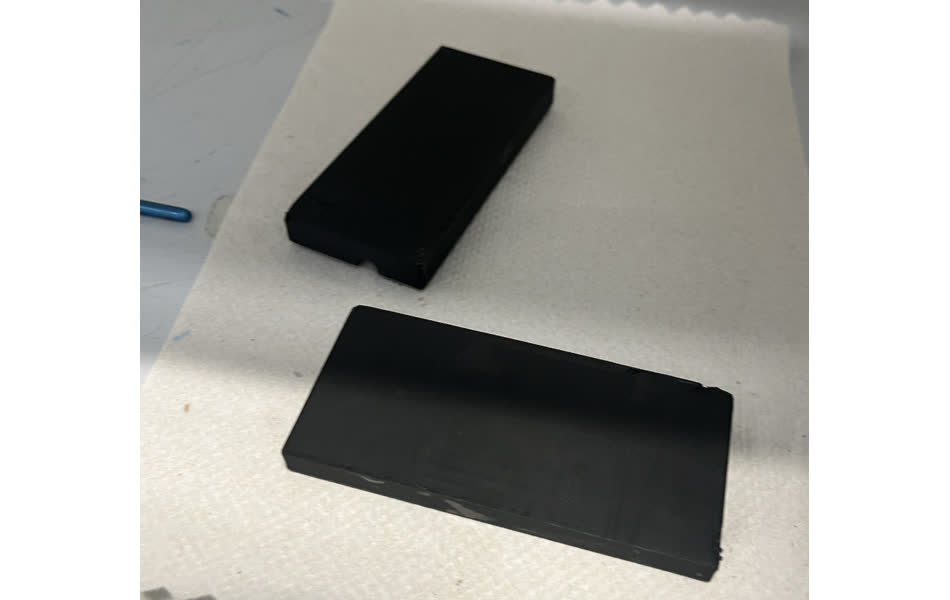
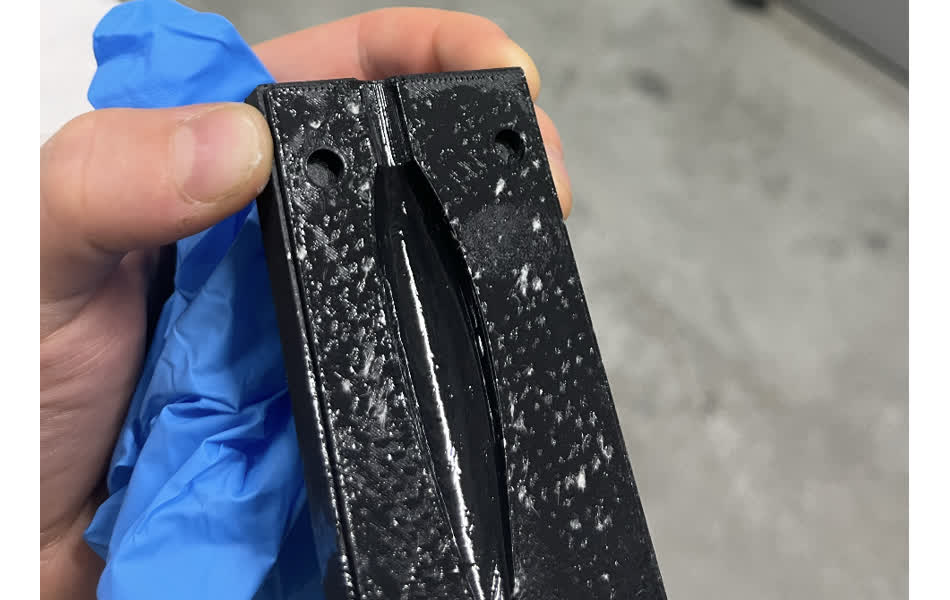
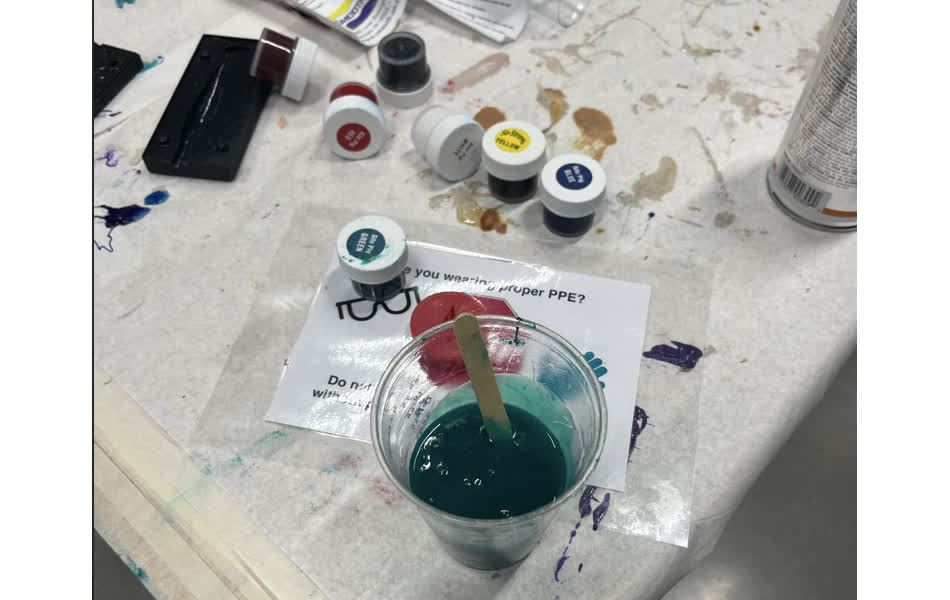
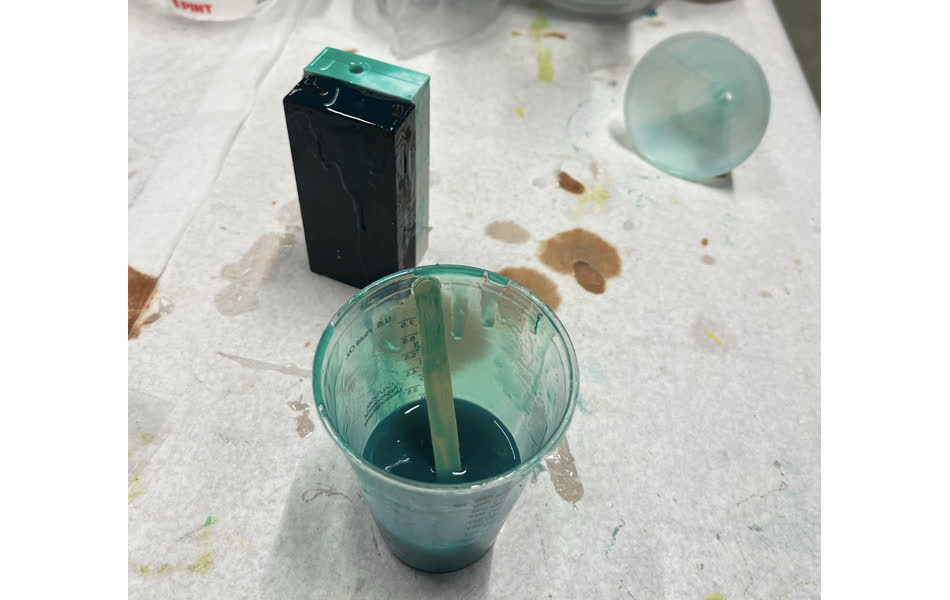
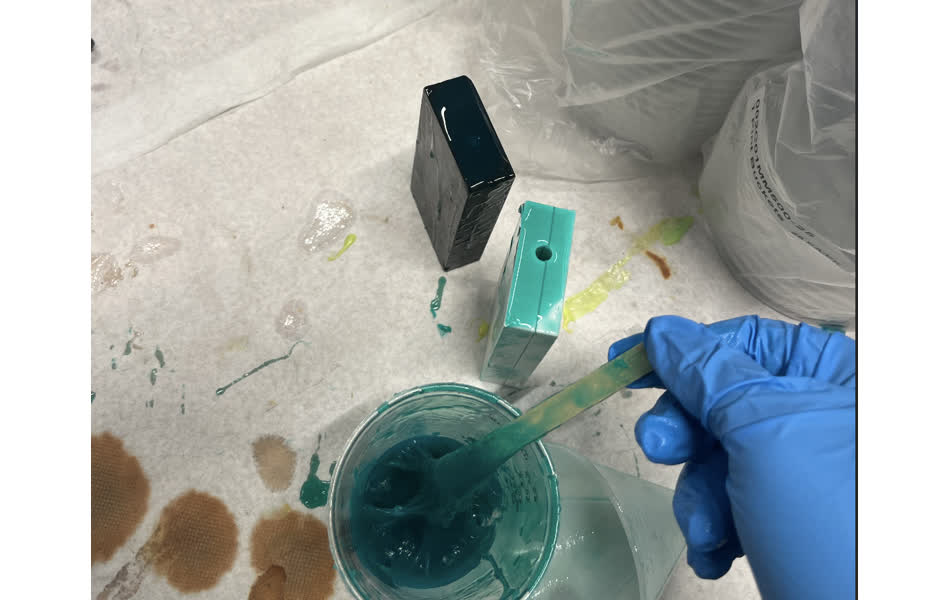
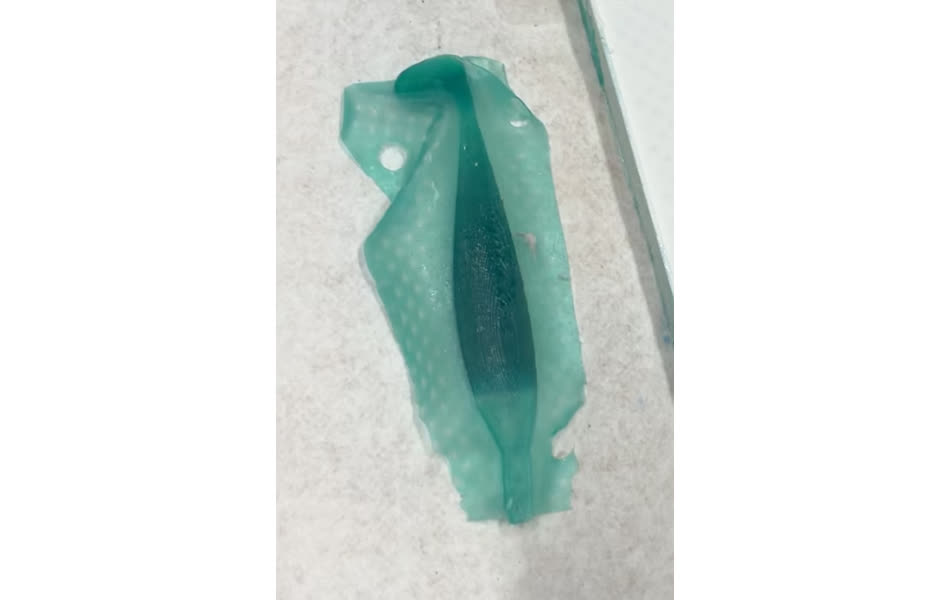
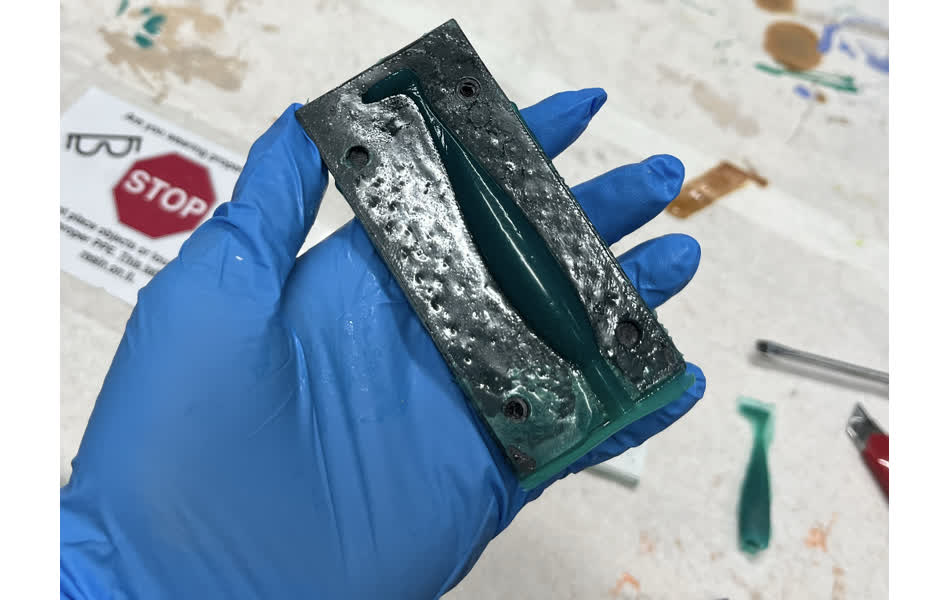
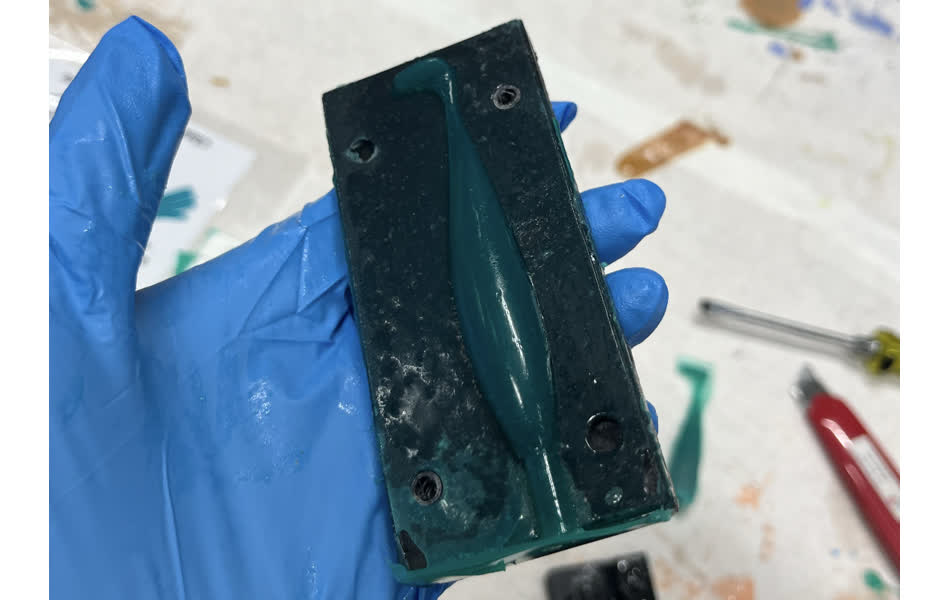
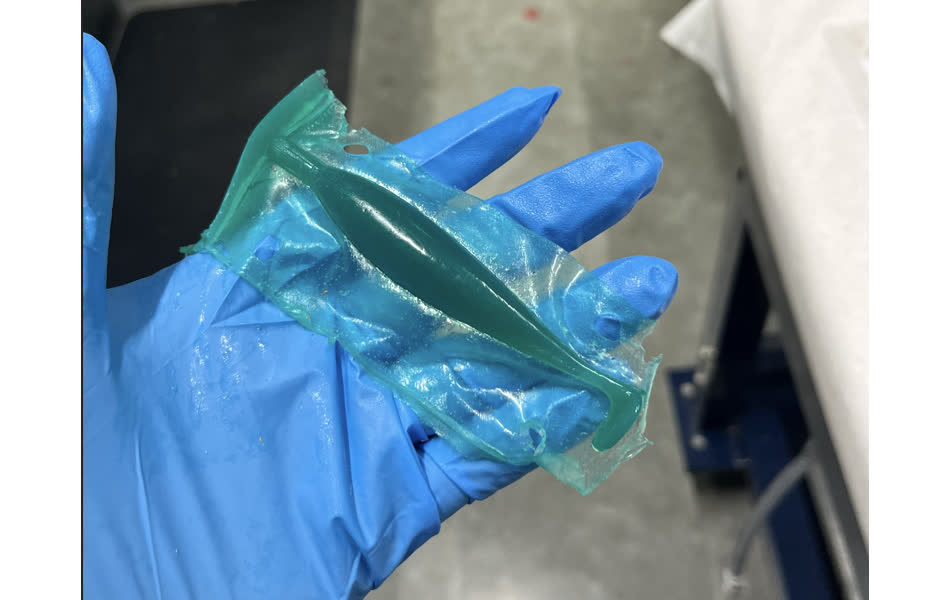
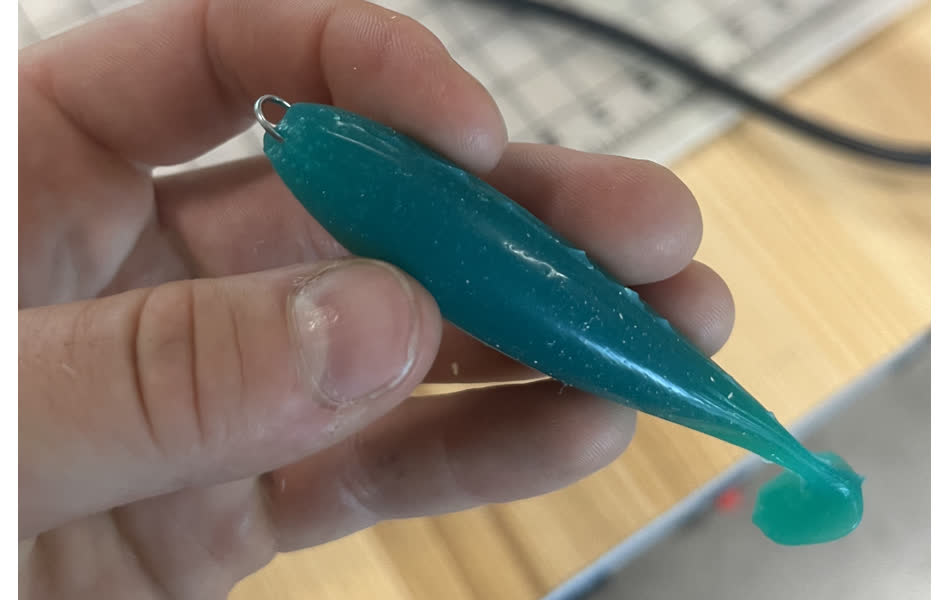
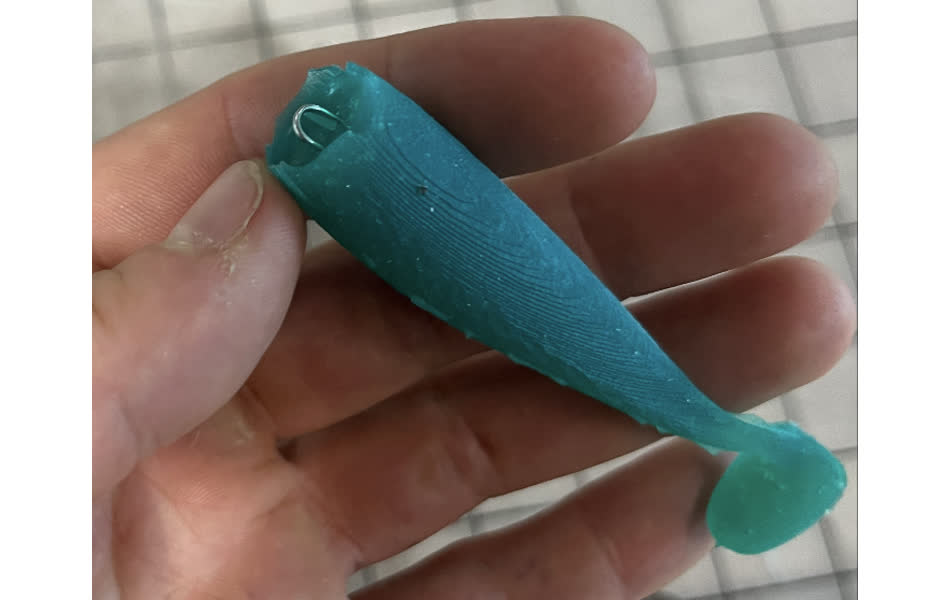
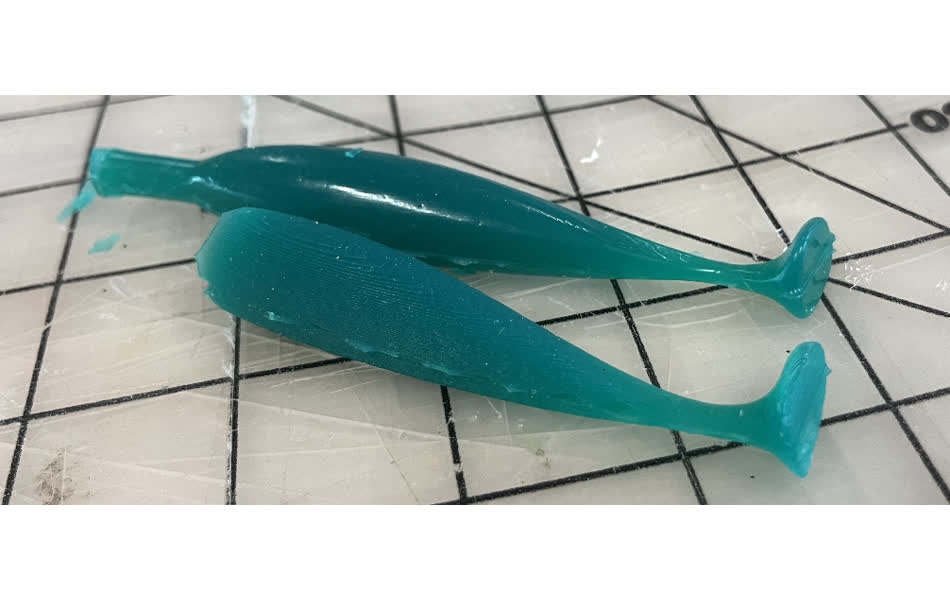