
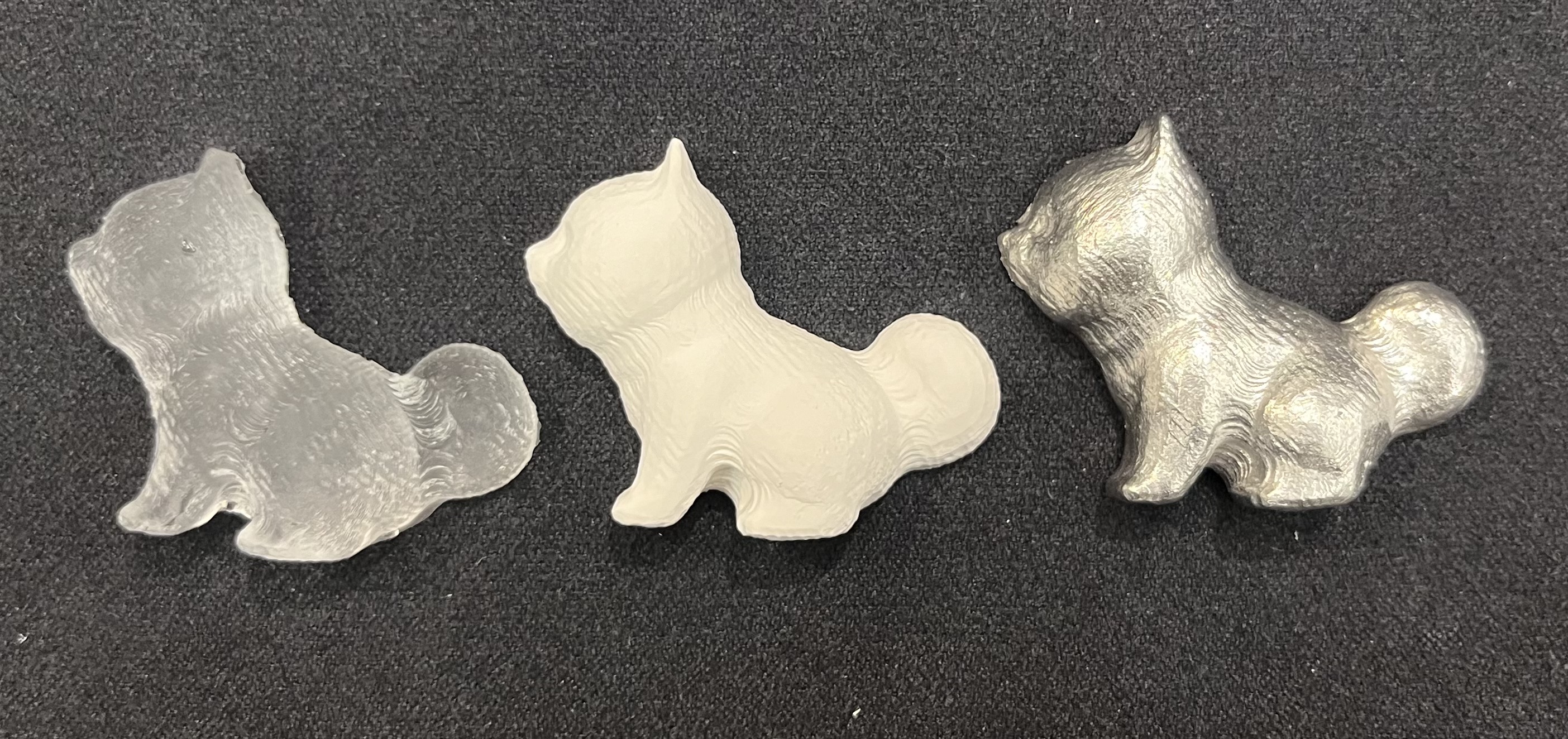
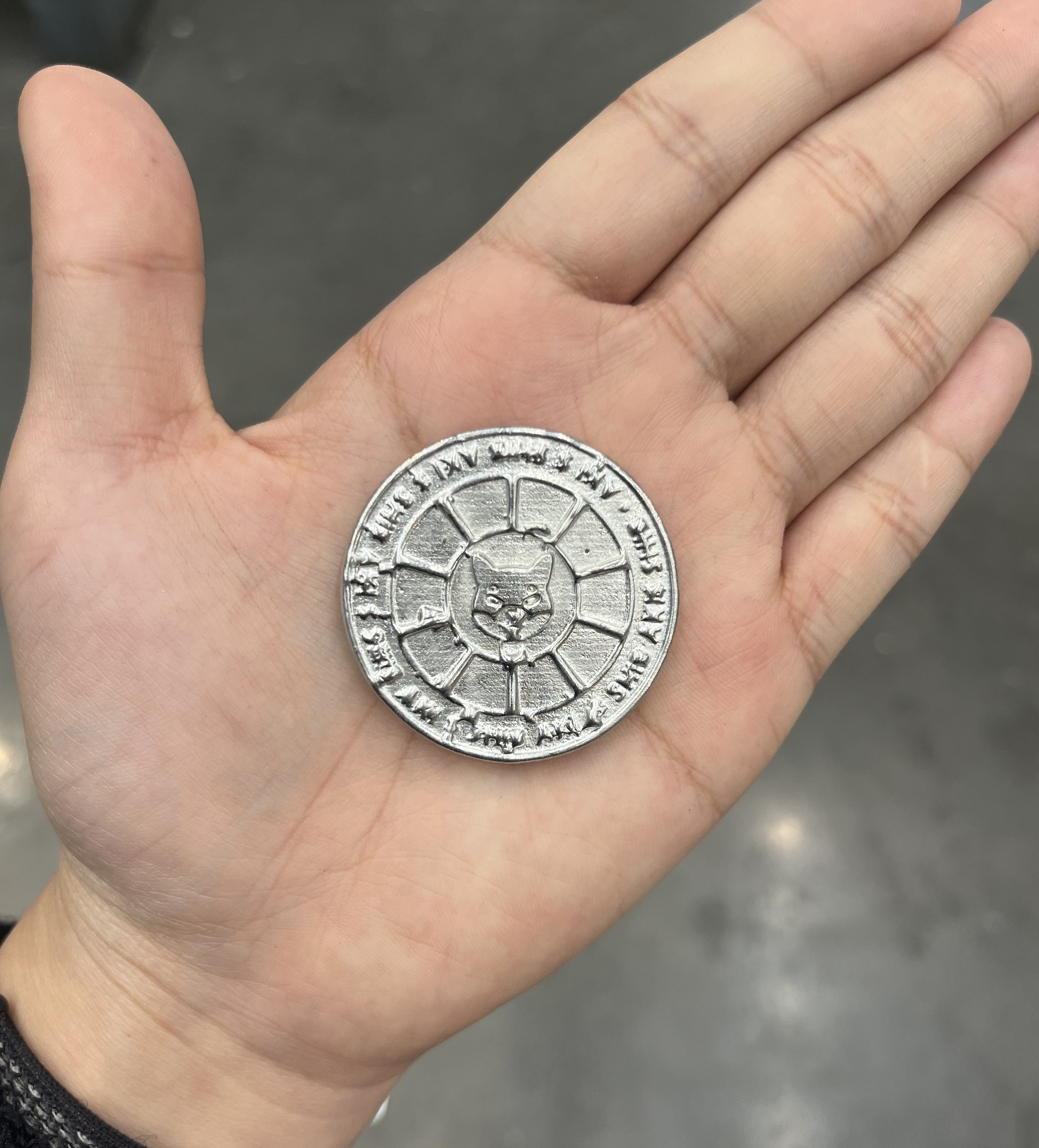
This week’s exploration delved into the fascinating world of mold and casting, leveraging the capabilities of a 3-axis CNC machine for wax milling as a negative mold and employing OOMOO to create a positive mold. In my experimentation, I ventured into utilizing various casting materials, including metal alloy, epoxy resin, and hydrocal. The following will serve as a comprehensive guide detailing the processes of creating molds using two distinct methods: the Wax Milling Mode and the One-Piece Mode.
File Links
Wax Milling Mold
Tools & Materials:
- 3-axis CNC machine
- Wax block
- OOMOO (A:B = 1:1 in volume)
Procedure:
- Set up the 3-axis CNC machine for wax milling.
- Mix OOMOO in a 1:1 volume ratio and pour it gently and evenly into the wax milling mold.
- Wait patiently and allow the mold to fully cure, typically following the manufacturer’s recommended curing time.
- Once the mold is completely cured, carefully release the model from the mold.
One-Piece Mold
Tools & Materials:
- 3D printed Machine
- Container
- OOMOO (A:B = 1:1 volume ratio)
- Sharp knife (with a zig-zag pattern on the cutting faces)
Procedure:
- Begin by preparing a 3D printed object that you wish to cast.
- Secure the 3D printed object to the bottom of a container. Ensure it’s firmly in place, as it will serve as the base for your mold.
- Mix OOMOO in a 1:1 volume ratio and pour it into the container, covering the 3D printed object completely.
- Allow the OOMOO to cure fully, adhering to the curing time recommended by the manufacturer.
- After the mold is fully cured, carefully remove it from the container.
(You now have a one-piece mold ready for casting.)
- To extract your casted object from the one-piece mold, use a sharp knife with a zig-zag pattern on the cutting faces. This will help in the molding alignment.
By mastering both the Wax Milling Mode and One-Piece Mode, you can explore a wide range of possibilities for creating intricate and unique casts using the negative and positive molds you’ve crafted. Be sure to experiment with various casting materials, as each offers distinct properties and aesthetics that can elevate your projects. Mold and casting techniques like these open up exciting creative avenues and empower you to bring your designs to life with precision and finesse. So, get ready to mold, cast, and let your imagination run wild in the world of fabrication!
3D printing for making OMOO mold
I also design a shiba coin, but I soon found out the end-mill for wax milling is too large for such detail design. So I 3D print the coin and mold it into an OOMOO mold. Though the OOMOO mold lost a lots of detail. The result metal coin is acceptable.
Take-a-way
If I can redo it again, I would directly 3D print the mold itself(the filiment can bear the heat of melting iron) and make the coin out of the mold.