how to (almost) make (almost) anything
mechanical machine design
For Mechanical Machine Design (Machine Week), the Architecture section designed and fabricated a capactive-touch controlled claw machine that grasps (and pops) balloons. This week is primarily documented here.
We divided ourselves among (4) teams:
- Claw
- Horizontal Axis
- Housing & Design
- Electronics & Coordination
By working in parallel, we were avoiding bottlenecks in production. To do so, we needed to agree on certain parameters (dimensions, for example). Since electronics would touch each part of the whole design, it was decided that electronics should also include the administrative and coordinating efforts. I've been interested in electronics design this semester and I thought I had enough project management experience to add value to this team.
I based the capacitive touch board off of Matt Blackshaw's example and added a button to control the claw grasp.
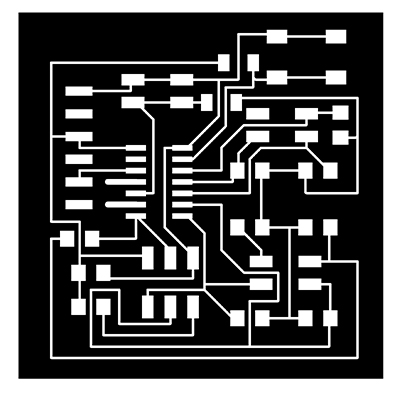
I milled the final board.
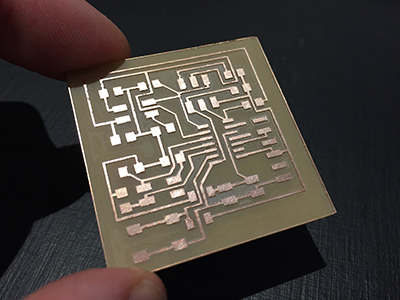
I co-designed and produced the capacitive touch interface, including the design and fabrication of a mock-up before the final production.
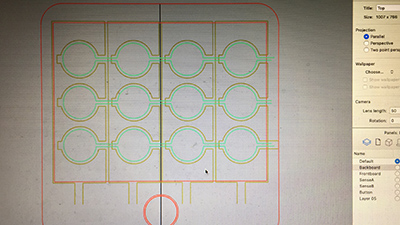
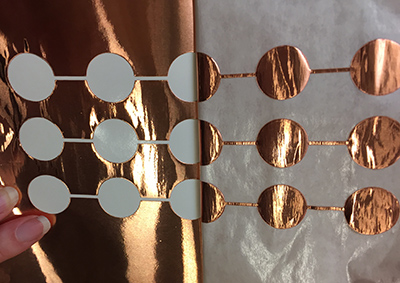
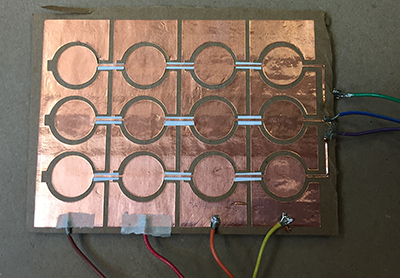
I milled the PCB that Team Claw had designed.

I tried Cuttlefish, but ultimately Morgan worked through this part by herself (and with Jake).
I kept a running task list to keep track of team and group goals, and communicated with each team for updates and coordination information.
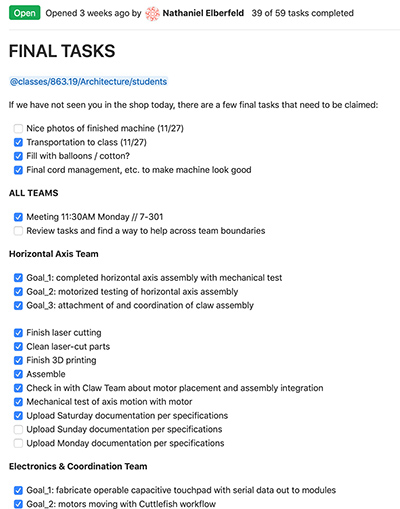
I helped with final assembly and testing, as all of the parallel projects came together. This was good discipline for the final project, which is similarly an assembly of many systems.