Mechanical & Machine Design
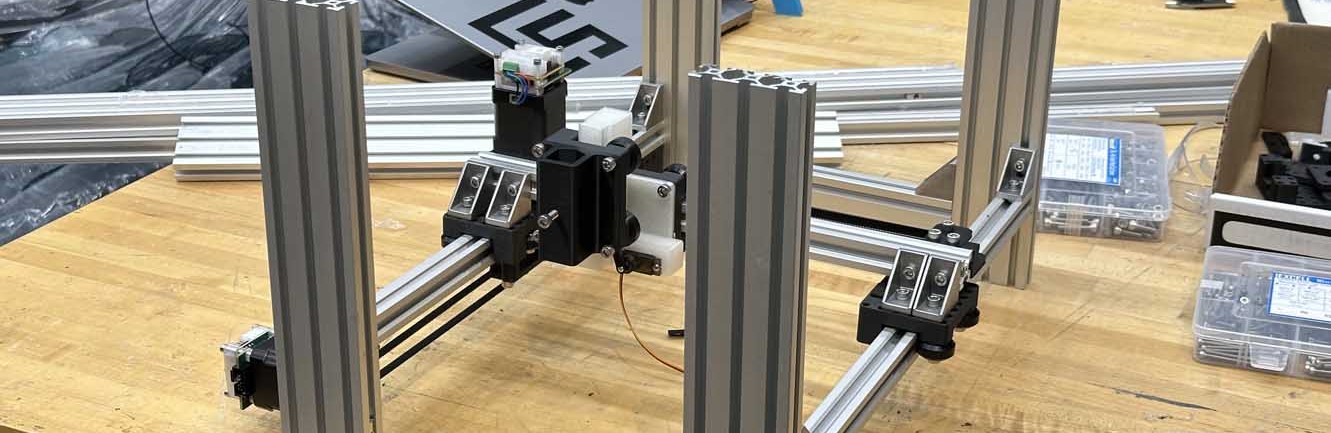
This week we deviate from the typical formula and collaborate within our lab sections to build a signle machine that automates a thing of our choosing. So, the 20 of us in the CBA section had a couple of brainstorming sessions to decide on a machine, but after much deliberation and no ground being made, we realized that the machine we should build is a machine to make decisions.
The concept here is simple: the user will write a list of things they are deciding between and feed that to the machine, the machine will flip a coin, read the coin flip, then begin downselecting the list by crossing off choices with a pen until one option remains. To tackle this as a group we split into a few subteams, each with dedicated team lead. I chose to join the mechanical engineering team given my background with the subject. Other teams include the embedded/electrical engineering team, software and UX team, documentation, and videography teams. I was considering branching out to a less familiar topic, such as software; however, I will be attending the Venus Exploration and Analysis Conference Sunday through Tuesday of the week, which means I need to contribute as much as possible on the front end of the project (and I can help with final touches on Tuesday night), and MechE is where I see myself having the most significant impact over the accelerated timeline.
This week is aimed at being an exercise in rapid prototyping to achieve a group goal. From this we don't need to make a final product complete with packaging and asthetics, just the rough form that accomplishes what we ask it to do. To begin the machine design process, I started with brainstorm that put form to function to make the design tangible and our converstations more targeted moving foward. Below is the initial sketch concept.
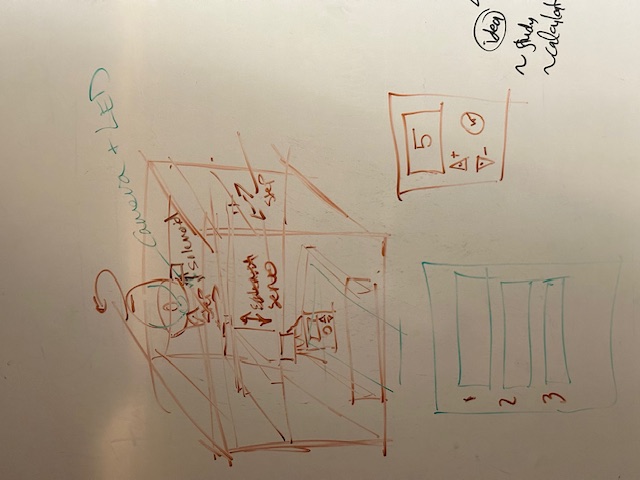
The major components of the machine are the rigid housing and paper tray, this subsystem will ensure the relative position of the decision list will remain more or less fixed in relation to the XYZ motion drawing mechanism. This subsystem, which interfaces mechanically to the rest of the system is a 2.5-axis CNC pen drawing machine. Initial consideration to achieve the appropriate DOF is using Core-XY and a servo for Z. Finally, a solenoid will fire to flip a coin that is contained in a clear housing. This housing is inspired by the board game "Trouble" such that the coin will bounce around in the hemisphere structure, and with clear walls on all sides, a camera will be set up to read the flip result using CV running on the attached laptop. Strictly speaking the coin flip mechanism doesn't need to be mechanically interfaced to the rest of the machine, but the inital concept has this as an ideal for the system to strive for. From this concept sketch I went to the lab and made a rough CAD of the sketch. Below is the CAD concept, this design has many floating structures and non-standard mates. This CAD serves as a better talking point for iterating the design and sparking next steps rather than providing an actual blueprint to follow - that will follow in a detailed design.
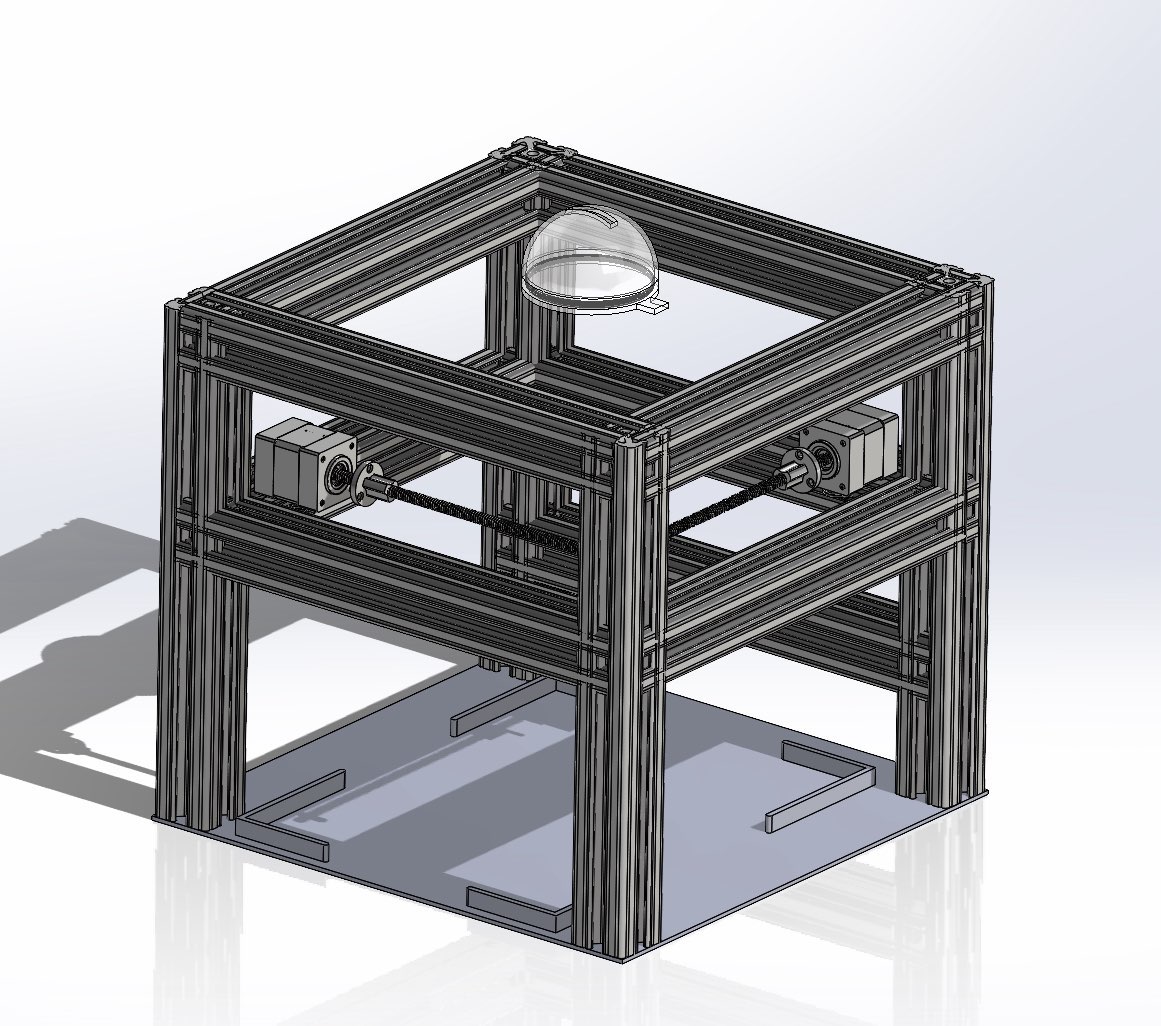

Upon iterating the CAD, it became clear that the next step needed by the mechE team is that we needed to assemble our XYZ motion machine and then design the rest of the interfaces around the keep-out/keep-in volume produced by the rapid construction of our Core-XY. When we got our hands on the hardware, it became clear that we required much less robustness and precision than Core-XY - that method is frankly overkill for this application. In it's place, we opted for a single belt/stepper driven rail and gantry system. This will minimize power and complexity. With this decision we decided to begin assemly and see how actuation goes. Below is our first attempt at actuating a single axis rail with a belt and stepper motor.
The ~1in of motion is perfect for our proof-of-concept. This shows how much additional space is needed on each axis for the support equipment. From this we chould begin cutting the 1x1 aluminum extrusions to build the XY-axis motion mechanism. With this made to spec, I tested my design and construction, shown in the video below.
Next up was building the Z motion and a rigid housing for the system. Jonny took on the servo actuation for the pen in Z and I finished out the XY motion + housing. I finished the gantry and rail system with roughly sized feet to test it's motion and allignment, shown below.

On Saturday, Jonny integrated the Z motion and I finished the rigid structure. Shown below is the final XYZ mechanical system for the drawing machine. This system comprises the majoriry of my personal contributions over the timeline I was able to contribute. Below is a video of me operating the X,Y,Z axes manally in the rigid body.After this I helped design revised coin flipping mechanisms since the solenoids were not proving to be a good fit for the target application. Dubbed the "Boinkinator" by Jonny (thanks), below is a concept sketch I made for creating a vibe box for the coin that would sufficiently jostle it and flip it around. With this, I needed to end my contributions in the lab and head to the VEXAG conference, but since I got us to a point where we can operate our machine manually, that accounts for about half of the assignment requirements, so I feel good about my level of contributions!

When I returned from the conference, I helped with finishing touches and saw the awesome work my group had done over the week. Most incredibly, the full integrated test of the machine happened where it chose its own name, "Decision Maker 9000." Iconic. No notes. We now live under the tyranny of this machine and can defer all decisions to it. Will I see you next week? I'll ask the Decision Maker 9000.